eaux ultrapures pour les industries des semi-conducteurs et de la pharmacie
Temps de lecture :Le traitement des eaux ultrapures ( EUP ) s’adresse essentiellement aux industries des semi-conducteurs, ainsi qu’à certains ateliers de l’industrie pharmaceutique. Vu l’importance croissante des recyclages dans la première de ces industries, il nous a semblé plus clair de traiter également dans ce sous-chapitre la problématique du traitement de leurs effluents et de leur réutilisation éventuelle.
chaîne de traitements des eaux ultrapures (EUP) pour l’industrie des semi- conducteurs
généralités
Utilisée par cette industrie comme agent de rinçage aux différentes phases de la production de ses composants, la qualité de l’eau est d’une importance critique pour le process de production (en relation directe avec les taux de rebut des mémoires, microprocesseurs et autres produits).
L’eau est pour cette industrie le fluide de nettoyage disponible en grande quantité et à des coûts raisonnables et doit le rester. Or, comme nous l’avons vu à la section eaux de fabrication (tableau 26), l’évolution vers la miniaturisation des composants produits exige des spécifications de plus en plus strictes sur tous les éléments solubles ou non pouvant se trouver dans une eau. Ces développements posent au traiteur d’eau des challenges de plus en plus difficiles mais que jusqu’à présent celui-ci a su relever.
De même, à qualité égale, lors de l’introduction en 2001 des tranches de silicium Wafer de 300 mm, il a fallu augmenter significativement de 4 à 5 m3 les débits d’EUP pour une tranche Ø 300 mm. Cette évolution porte les demandes en EUP d’une installation type à 100-300 m3·h–1.
spécifications et concept de traitement en résultat
Les principales impuretés à éliminer sont les MES, les particules, les bactéries, le COT, l’oxygène dissous, l’ensemble des ions dont, parmi eux, les plus difficiles : la silice et le bore, et ceci comme précisé dans l’extrait du tableau 3 au niveau des ppb et jusqu’aux ppt (1 mg par 1 000 m3) pour la plupart des ions.

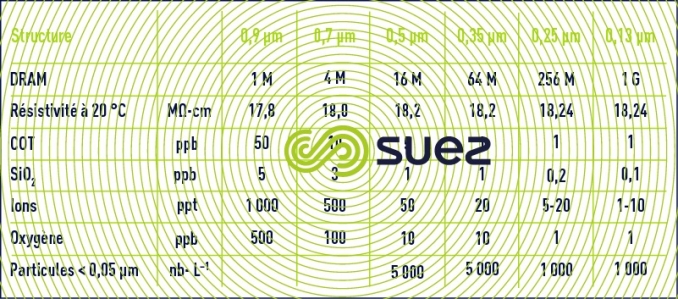

En conséquence, les lignes de traitement associent plusieurs étapes dans lesquelles les membranes jouent un rôle prépondérant.
Les figures 13, 14, 15, montrent, sur une installation typique réalisée en Malaisie pour 1 st Silicon, une FAB de technologie 180/130 nm, les systèmes de :
prétraitement (figure 13)
L’eau y est filtrée sur filtre bicouche puis sur charbon actif et enfin adoucie sur résine cationique, ceci afin de limiter les risques de fouling et d’entartrage de l’osmose inverse 1. Cette étape dépend bien évidemment de la qualité d’eau brute disponible (ici, une eau de surface).

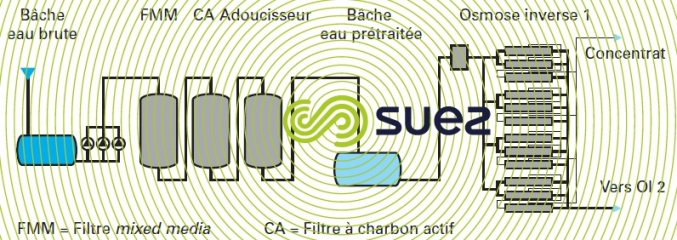


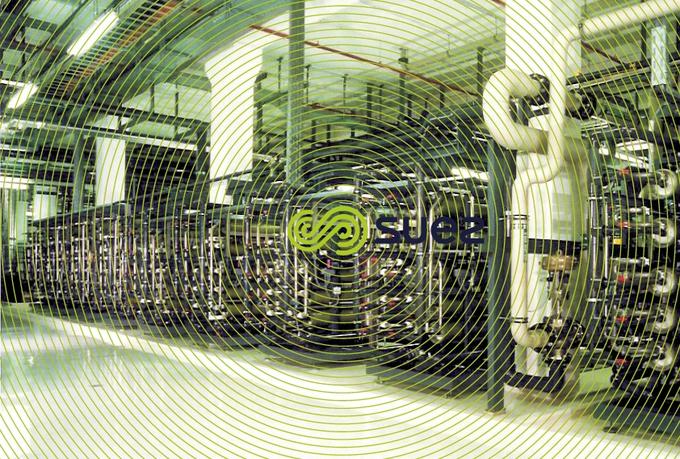

traitement deau dappoint (figure 14)
Il comporte une deuxième osmose travaillant en « 2e passe » (voir séparation par membranes) et permettant à ce stade, d’avoir éliminé de 99 % à plus de 99,99 % de pratiquement tous les ions, matières organiques, particules… Le perméat est stocké dans une bâche où il est ozoné (stérilisation et oxydation de MO) puis pompé vers des UV à 150 nm pour détruire l’ozone résiduelle et finir l’oxydation du TOC (voir oxydation et réduction). Un dégazeur sous vide élimine l’essentiel du CO2 et de l’oxygène (teneur résiduelle < 10 ppb). Le reste des ions ayant traversé les deux osmoseurs ou ayant été créés par l’oxydation à l’ozone puis par les UV sont éliminés par des lits mélangés à régénération externe, permettant une régénération poussée des résines en évitant tout risque de repollution de l’eau par les réactifs de régénération.
À l’aval des lits mélangés, on doit obtenir une conductivité très proche de la valeur théorique de 0,055 μs·cm–1 (18,2 MΩ·cm–1 à 20 °C).

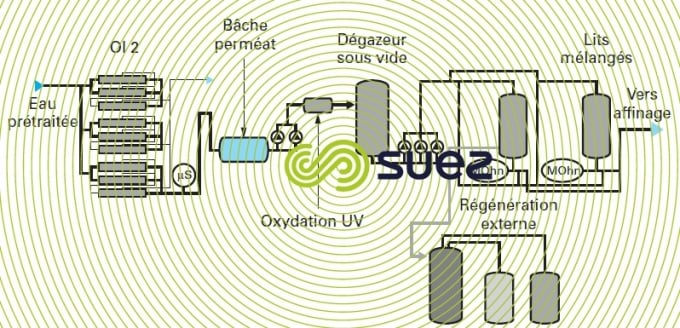

boucle daffinage et de distribution (figure 15)
Cette boucle fermée sur la bâche d’EUP (sous azote) permet de maintenir :
- une distribution dans laquelle l’eau tourne en permanence, évitant ainsi tout point de stagnation (lieux de recolonisation bactérienne…) ;

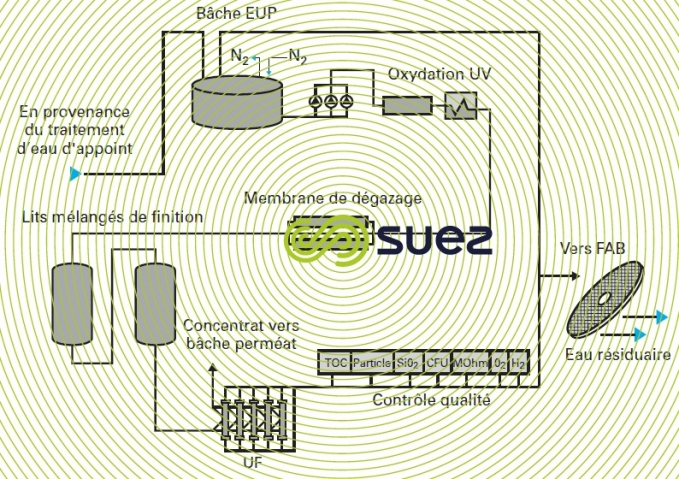

- la qualité de celle-ci grâce à une nouvelle oxydation UV, un dégazage des derniers ppb d’O2 et de CO2 sur une membrane de dégazage, puis des mixed-bed non régénérables installés sur cette boucle.
Une filtration sur ultrafiltres (photo 7) juste avant les points de soutirage assure l’élimination finale des particules jusqu’à moins de 1 particule > 0,05 μm par mL. Après les ultrafiltres, la qualité de l’eau est suivie en continu : au minimum son COT, ses particules, sa conductivité et sa teneur en silice.
contraintes supplémentaires
fonctionnement continu
Celui-ci est absolument nécessaire comme déjà vu, tout fonctionnement discontinu fait varier la qualité physique, chimique et biologique de l’EUP (détache des particules, permet les recolonisations bactériennes, tasse, détasse les résines…).
modularité
Pour assurer aussi bien la continuité de fonctionnement que les délais de mise en service, les systèmes d’EPU doivent être conçus sous forme d’éléments modulaires, prémontés en atelier sur skid (photos 6 et 7) et aussi compacts que possible afin :
- d’assurer facilement une redondance permettant un service totalement continu – 0 arrêt pour maintenance… (un module de chaque type en stand-by)
- de faciliter les extensions souvent prévues ;
- de minimiser les délais : vues les tensions sur le prix des DRAM, les producteurs cherchent à réduire au minimum le temps s’écoulant entre la décision de produire un nouveau produit (ou sur un nouveau site) et sa mise sur le marché. La modularité et le montage dans les ateliers du fournisseur sont ainsi devenus deux conditions rédhibitoires. À noter pour celui-ci la contrainte d’avoir des salles blanches (photo 8) pour le montage, la disponibilité d’EUP pour rincer tout le système, d’azote pour le maintenir sous azote…
Au cours du temps, ces contraintes ont toutes les chances de s’aggraver, ce qui, au niveau du choix des outils de traitement, pousse vers des outils modulaires, facilement permutables, facilement rinçables, avec au premier rang les systèmes membranaires, pour lesquels une sélection sévère des membranes doit être faite, en particulier afin de s’assurer de leur intégrité.

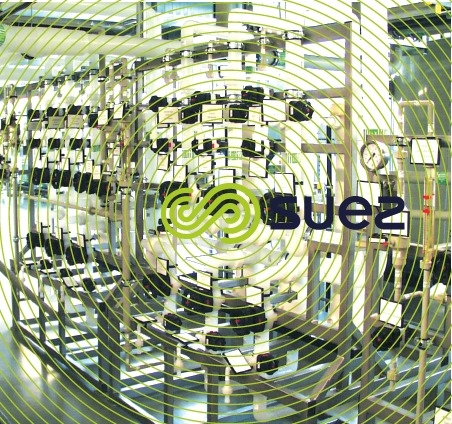


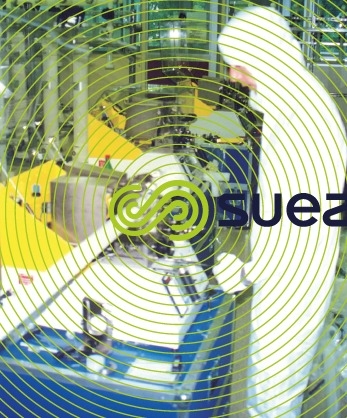

traitement des effluents de l’industrie des semi-conducteurs
généralités
D’abord parent pauvre des EUP, le traitement des effluents devient de plus en plus important sous l’influence de standards de rejet plus stricts mais aussi de l’apparition de nouveaux types de rejet correspondant à de nouveaux procédés de fabrication qui, en conséquence, rendent leur traitement plus complexe.
Une unité de fabrication moderne comprend les effluents suivants répartis en cinq réseaux :
- effluents acides et basiques ;
- effluents contenant de l’acide fluorhydrique (HF) ;
- effluents des polissages chimiques et mécaniques (CMP) comportant des MES, colloïdes…;
- effluents des CMP contenant en outre du cuivre ;
- effluents contenant de l’ammoniaque et des MO.
Suivant les contraintes environnementales, ces effluents devront être prétraités spécifiquement, puis en général neutralisés en commun.
exemple de réalisation
La société STMicroelectronics (Crolles – France) s’est équipée d’un nouveau système de traitement comportant des effluents de tous les types ci-dessus mentionnés.
Le schéma de traitement utilisé est celui des figures 16 et 17.

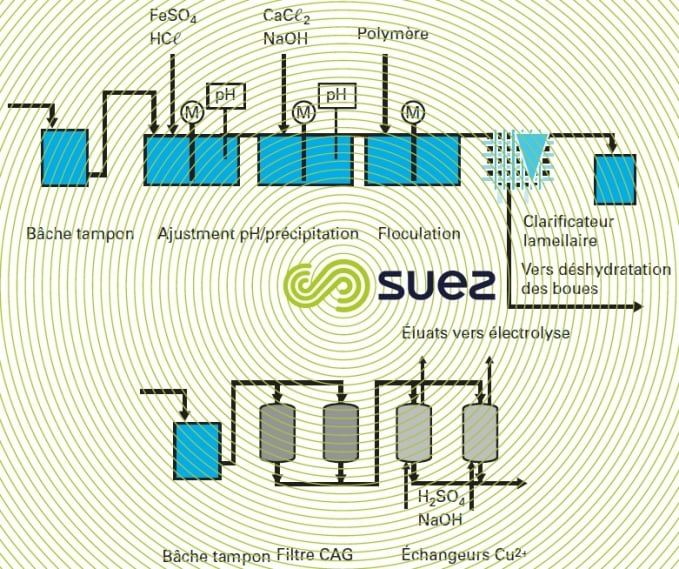


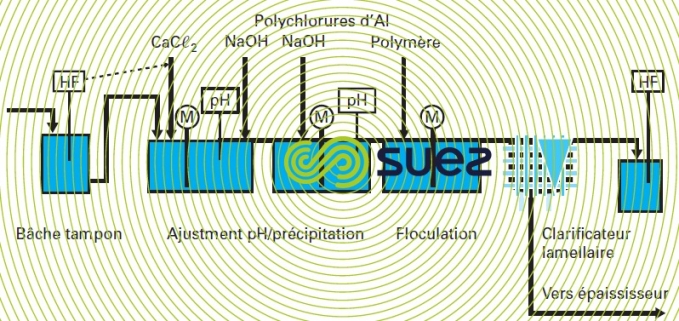

traitement des effluents CMP contenant du cuivre (figure 16)
par précipitation coagulation-floculation et séparation sur clarificateur lamellaire puis élimination des MO sur charbon actif et du cuivre sur échangeur d’ions sélectif (Cu < 0,1 ppm).
Remarque : le cuivre est récupéré par électrolyse dans les éluats de régénération.
traitement des eaux avec HF (figure 17)
par précipitation de celui-ci ainsi que des phosphates par CaCℓ2 et clarification.
traitement des eaux ammoniaquées
par voie biologique : des Biofor permettent l’élimination des MO (essentiellement alcools biodégradables) avec nitrification et dénitrification de NH4+ soit trois étapes de cultures fixées (voir les processus élémentaires du génie biologique en traitement de l'eau et procédés biologiques). Enfin, les effluents sont mélangés et envoyés à une neutralisation et une filtration finale de sécurité avant rejet en rivière.
recyclage – réutilisation dans l’industrie des semi-conducteurs
généralités
Dans le monde des semi-conducteurs, recyclage et réutilisation sont un sujet de débat. En effet:
- vu la qualité exigée, tous craignent les risques de pollution apportés par les eaux résiduaires même « bien traitées » ;
- par ailleurs, il est évident qu’une grande partie de l’EUP, servant de fluide de rinçage à des composants peu contaminés, a des niveaux de contamination bien inférieurs aux eaux brutes disponibles (même lorsqu’il s’agit d’eau potable) et que la ségrégation de ces eaux de rinçage et leur retraitement peuvent être très économiques.
On notera que seul l’emploi de capteurs précis et fiables permet de concilier craintes des premiers et économie potentielle.
contraintes
De ce qui précède découlent les contraintes suivantes pour le traitement de recyclage :
- les procédés doivent être fiables et redondants ;
- la qualité et la disponibilité de l’EUP ne doivent à aucun moment être mises à risques par la réutilisation. Ceci implique entre autres que toute substance qui ne peut être éliminée parfaitement par le traitement principal des EUP doit impérativement être éliminée spécifiquement avant envoi à la bâche de recyclage.
Par ailleurs, suite à des sécheresses, les autorités de certains pays ont imposé récemment un recyclage allant jusqu’à 85 % pour limiter les prélèvements dans le milieu naturel et nous ont ainsi obligés à mettre au point des systèmes répondant à cette exigence.
La figure 18 montre l’organisation et le bilan eau d’une installation recyclant plus de 85 % de ces effluents. Ce schéma montre entre autres que l’impact est général et touche tous les circuits. En outre :
- la concentration des rejets résiduels est évidemment accrue ;
- le traitement d’EUP travaille sur une eau de caractéristiques très différentes (beaucoup moins de sel, plus de particules…) ;
- par ailleurs, tout changement de processus de fabrication impactera le traitement des effluents et donc le traitement d’EUP imposant un dialogue permanent producteur-fournisseurs.

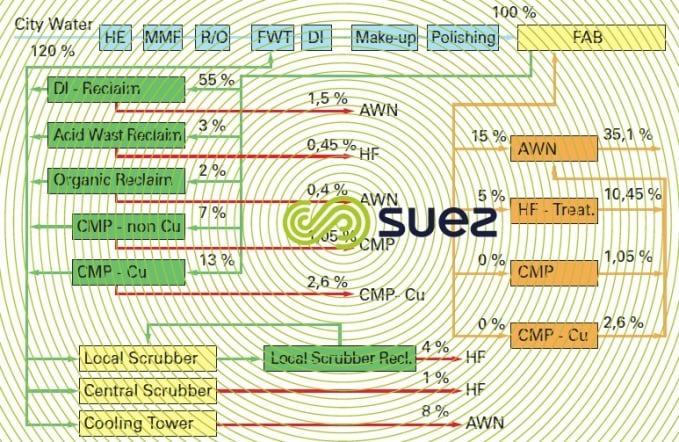

technologie
Les chaînes de traitement des eaux de rinçage après vérification de leur contamination limitée sont traitées de la manière suivante :
- les MES et colloïdes provenant des CMP sont éliminés sur membrane d’UF ;
- les ions sont passés sur échangeurs d’ions (chaîne Af – CaF – AF) ;
- l’alcool isopropylique ( AIP ), principale matière organique présente, est éliminé sur biofiltre, suivi en général de filtration sur multimédia, charbon actif et osmose inverse (figure 19).
Ainsi, leur recyclage devient possible en tête de la boucle d’appoint des EUP.

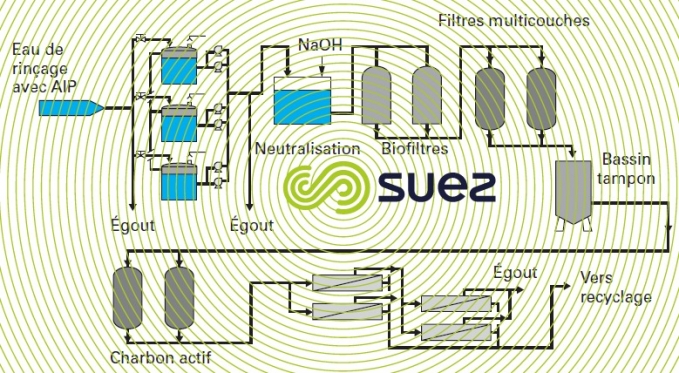

eaux pour les industries pharmaceutiques
généralités
Les demandes en terme de qualité d’eau varient beaucoup suivant les procédés de fabrications. On distingue usuellement :
- « les eaux purifiées » (PW) ;
- « les eaux pour injection » (WFI) dont les qualités sont définies réglementairement : normes GMP en Europe, FDA aux États-Unis…
On notera que les besoins en eau de grande qualité sont plus limités que dans l’industrie électronique, en général de 5 à 50 m3·h–1.
Les règlements GMP visent non seulement la qualité finale, mais également les moyens mis en œuvre pour l’obtenir, ce que nous savons faire en utilisant en particulier des systèmes membranaires d’osmose et de dégazéification et d’électrodésionisation (voir procédés de perméation et membranes de dialyse) pré-assemblés et utilisant sur ceux-ci les matériaux, capteurs et systèmes de commande et surveillance automatiques requis avec toutes les certifications nécessaires.
contrainte des EUP pour l’industrie pharmaceutique
Les qualités requises, qui sont donc définies par les Codex nationaux (pharmacopées), diffèrent peu, comme le montre le tableau 4, qui compare les situations européenne et américaine (dans les deux cas, il est précisé que l’eau brute utilisée est de l’eau potable).

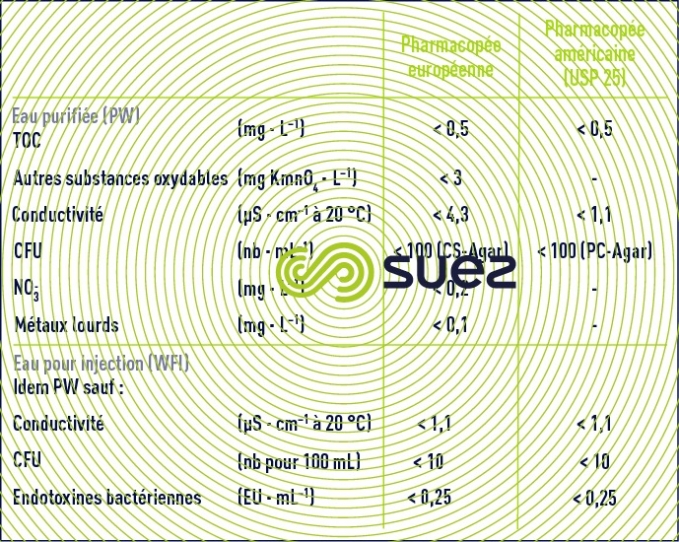

procédés utilisés
Pour obtenir une conductivité inférieure à 1,1 μs · cm–1, il faut une osmose à deux passes avec un système de dégazage du CO2. Dans certains cas d’eau potable très saline, la deuxième passe doit être remplacée par une EDI donnant facilement 0,5 μS · cm–1. Les coûts d’investissement de la combinaison OI + EDI (système Rocedis) sont légèrement plus élevés que ceux d’une osmose double passe, mais les coûts de fonctionnement sont comparables. Aussi, cette combinaison OI + EDI produisant des eaux de meilleure conductivité est de plus en plus souvent choisie.
prétraitements
Le but du prétraitement est de protéger l’osmose inverse située à l’aval. Il dépend de la qualité de l’eau potable utilisée. Un procédé d’adoucissement sur résine est souvent recommandable pour éviter l’entartrage ou les salissures par les métaux résiduels (Aℓ, Fe, Mn…) et, en général, une déchloration s’impose.
osmose inverse ou combinaison OI + EDI
La conductivité de sortie est influencée par deux facteurs, la conductivité et le TAC de l’eau brute. En effet, le CO2 dissous (dépendant du pH) n’est pas retenu par les membranes d’osmose. Il faut donc, soit travailler à pH élevé après adoucissement poussé, soit utiliser une membrane de dégazage.
Ensuite, une deuxième passe d’osmose ou une EDI s’impose. Ce deuxième schéma est illustré par la figure 20 où 98 % du perméat de l’osmose est récupéré à une qualité supérieure à 16 MΩ·cm (< 0,065 μS · cm–1), les 2 % du concentrat pourront être recyclés. L’énergie nécessaire à l’EDI (Contipur) utilisée est d’environ 20 % inférieure à celle d’une deuxième passe équipée de modules basse pression. Le CO2 étant mal éliminé par l’EDI, il est conseillé de l’éliminer du perméat de l’osmose via un dégazeur à membrane.
L’eau purifiée est envoyée dans une boucle de distribution sur laquelle un UV oxydant et de l’ozone permet de maintenir de très faibles valeurs en MO et en bactéries.

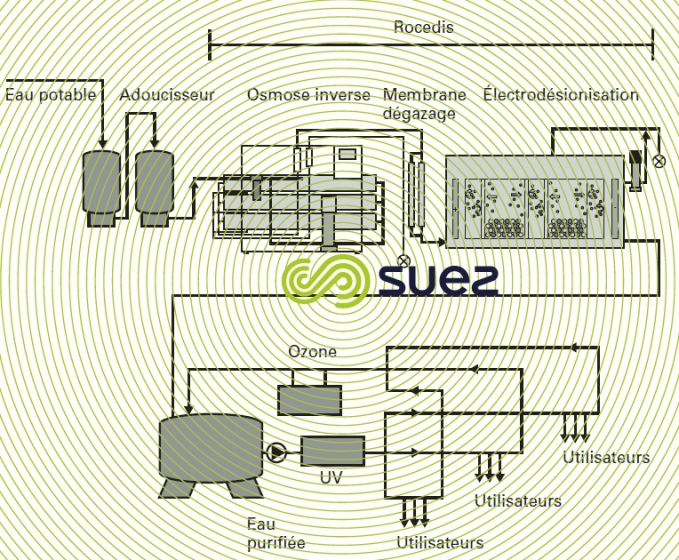

exemple
Une chaîne telle que décrite figure 20 permet de garantir sans problème les valeurs du tableau 5 où l’on constate en particulier les valeurs excellentes obtenues sur l’élimination des endotoxines (< 0,1 EU · mL–1) malgré une eau potable très riche (~ 20 EU · mL–1), ce qui représente 99 % d’élimination sur l’osmose et > 50 % sur EDI. La photo 9 illustre un skid en fonctionnement.

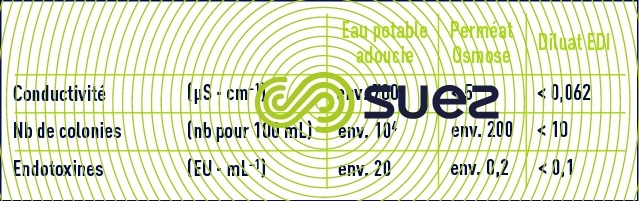


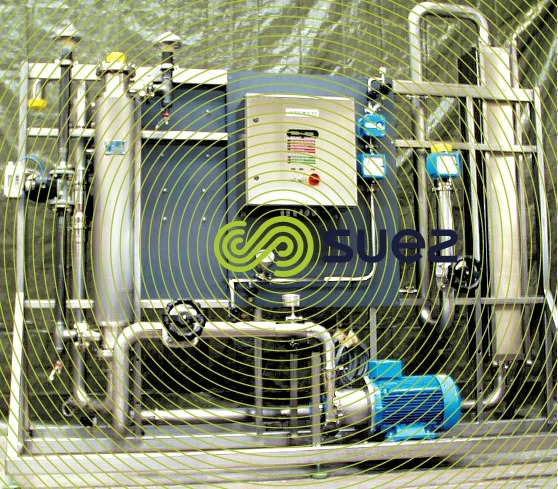

Outil Marque-page
Cliquez sur l'outil marque-page, puis surlignez le dernier paragraphe lu pour pouvoir poursuivre ultérieurement votre lecture.
