eaux de fabrication
Temps de lecture :Les besoins et contraintes en eau de refroidissement et eaux de chaudières sont généraux pour tout type d’industrie, elles peuvent faire, comme vu ci-dessus, l’objet de recommandations « interprofessionnelles » ou au contraire, les eaux de fabrication sont propres à chaque industrie, elles seront donc étudiées par type d’industrie.
Par ailleurs, le les effuents industriels du même chapitre traite des effluents produits par les mêmes industries, un certain nombre de recoupements sont à faire (quantité d’eau nécessaire, description des procédés utilisateurs d’eau qui sont en général les mêmes que ceux producteurs d’effluents…).
eaux de brasseries et boissons gazeuses
brasseries
utilisations
- préparation de la bière ;
- lavage des cuves, appareils et sols ;
- refroidissement ;
- éventuellement nettoyage des bouteilles.
qualité des eaux d’appoint
Elles font l’objet de recommandations professionnelles très dépendantes des qualités de bières élaborées. Ainsi les bicarbonates qui précipiteraient lors de l’introduction du malt riche en phosphate de calcium sont à éviter en brassage.
On peut en première approche retenir les règles suivantes :
- élimination systématique des bicarbonates (précipitation ou acidification et dégazage) ;
- concentration en Mg aussi faible que possible (< 10 mg·L–1) ;
- rapport SO4/Cℓ supérieur à 1 (moelleux des bières) ;
- concentration en Na < 100 mg·L–1 pour minimiser l’âcreté ;
- NO3 < 50 mg·L–1 et NO2< 1 mg·L–1 (limites de potabilité et de toxicité en fermentation).
quantités mises en œuvre
3 à 5 hL par hL bière dont :
- préparation de la bière : 1,5 ;
- lavages : 1,5 à 3 ;
- refroidissement : 1 à 2.
boissons gazeuses
1 à 5 L d’eau sont nécessaires par litre de boissons, une partie de cette eau est incluse dans le produit fini et doit donc au minimum satisfaire les normes d’eau potable.
Les industriels continuent d’optimiser cette quantité d’eau utilisée, certains se rapprochant d’un rapport 1L d’eau pour 1L de produit fini.
Les fabricants définissent souvent eux-mêmes les qualités spécifiques de l’eau. Parmi celles-ci, on peut rechercher le maintien d’un TAC inférieur à 5 °F et une salinité totale inférieure à 500 mg·L–1. Pour les utilisations de l’eau en nettoyage, on peut en revanche demander un excès de chlore résiduel de plusieurs mg·L–1.
eaux minérales et eaux de source
Les eaux minérales naturelles, les eaux de source et les eaux de table embouteillées ont une législation spécifique qui peut être plus rarement moins contraignante que celle des eaux potables.
En sus, il convient d’éliminer tous les éléments instables susceptibles de précipiter dans les bouteilles lors de leur stockage, tels que le fer ou le manganèse.
industries laitières
L’eau est utilisée pour :
- désinfection des appareils et cuves ;
- nettoyage des sols ;
- lavage des produits ;
- reconstitution de lait ;
- chaudières et refroidissement.
Les utilisations diverses d’eau représentent 1 à 5 L par litre de lait.
sucreries et raffineries de sucre
sucreries de betteraves
Les techniques de traitement d’eaux industrielles interviennent dans l’épuration de l’eau d’appoint et du jus lui-même. Le graphique figure 18 montre un schéma simplifié des différents circuits d’une raffinerie de betteraves. Grandes utilisatrices d’eau, les sucreries ont peu à peu réduit leur consommation en utilisant de nombreux recyclages et réutilisations internes :
- lavage des betteraves : recyclage des eaux polluées via des décanteurs raclés ;
- diffusion des cossettes (préparation du jus brut) : traitement des eaux condensées ammoniacales pour recyclage en tête de diffusion.
- traitement des jus légers :
- décalcification des jus de deuxième carbonatation (protection contre le tartre des appareils d’évaporation) ;
- déminéralisation des jus (réduction du taux de mélasse) ;
- décoloration des sirops sur charbon actif ou résines adsorbantes ;
- concentration des jus, cristallisation du sucre avec conditionnement des jus dans les évaporateurs ;
- traitement des bas produits (égouts ou mélasses) en vue de réduire le taux de sucre-mélasse (perte de sucre) :
- traitement des égouts sur résine cationique régénérée au chlorure de magnésium (procédé Quentin). Le remplacement des ions Na et K par Mg réduit le sucre retenu dans la mélasse ;
- déminéralisation des égouts ou mélasses par échange d’ions, avec traitement complémentaire éventuel pour l’obtention de sucre liquide ;
- eaux d’appoint :
- appoint aux chaudières à l’ouverture de la campagne sucrière ou en cas d’insuffisance accidentelle des retours de condensats ;
- appoint permanent au circuit de refroidissement des turboalternateurs et à la réception des betteraves.
Sachant que la betterave contient environ 77 % d’eau, la sucrerie a un cycle excédentaire en eau comme illustré par la figure 18.

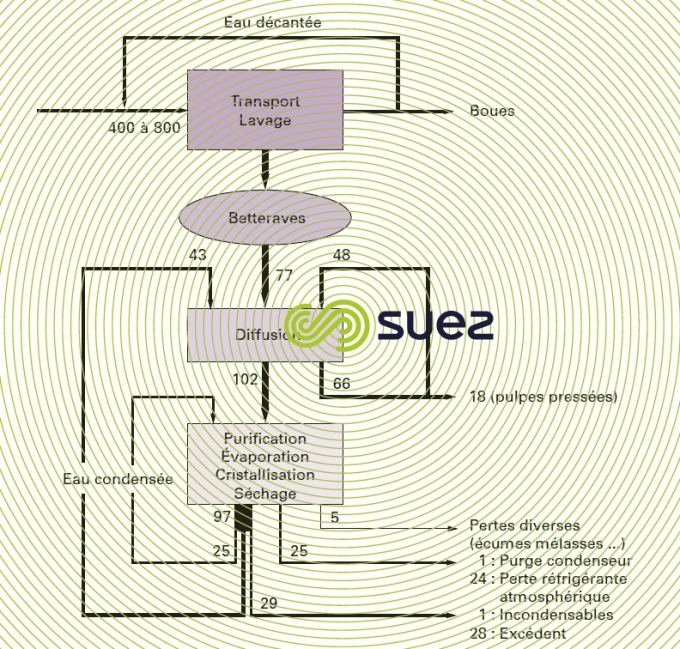

On notera que, dans les 28 m3 excédentaires, en fait 10 m3 sont recyclés au lavage des betteraves, 8 m3 sont utilisés pour divers lavages et en appoint des chaudières, 10 m3 seulement sont retournés au milieu naturel.
sucreries de canne
La purification des jus bruts requiert des méthodes de clarification analogues à celles de l’eau :
- décantation accélérée des jus « déféqués » à la chaux ;
- flottation des jus épurés en vue de séparer les « folles bagasses » ;
- désinfection des circuits (essentielle).
raffineries de sucre (betteraves ou canne)
Les sirops de refonte et les sucres liquides doivent subir des traitements de décoloration plus ou moins complets.
conserveries de légumes et de fruits
Il faut 5 à 40 m3 d’eau par tonne de conserve, utilisée pour le lavage, le pelage, et le blanchiment des légumes.
Un adoucissement au moins partiel des eaux de fabrication est souvent nécessaire. Mais une réduction de la salinité totale peut s’avérer utile, pour éviter la corrosion des boîtes.
industries textiles
L’eau est utilisée pour les chaudières (appoints souvent importants), pour les fabrications (teintures, rinçages) et pour le conditionnement de l’air (humidification et dépoussiérage).
Ces industries demandent de grandes quantités d’eaux, tableau 22 où l’on constate des différences marquées suivant les fibres traitées, objet des traitements suivants :
- eaux adoucies ou déminéralisées destinées à la préparation du fil, spécialement lorsqu’il s’agit de textiles artificiels ;
- eaux adoucies souvent décarbonatées destinées au blanchiment et à la teinture des fibres ;
- eaux déminéralisées pour conditionnement de l’air des salles de filature ou de tissage (osmose inverse, échange d’ions).

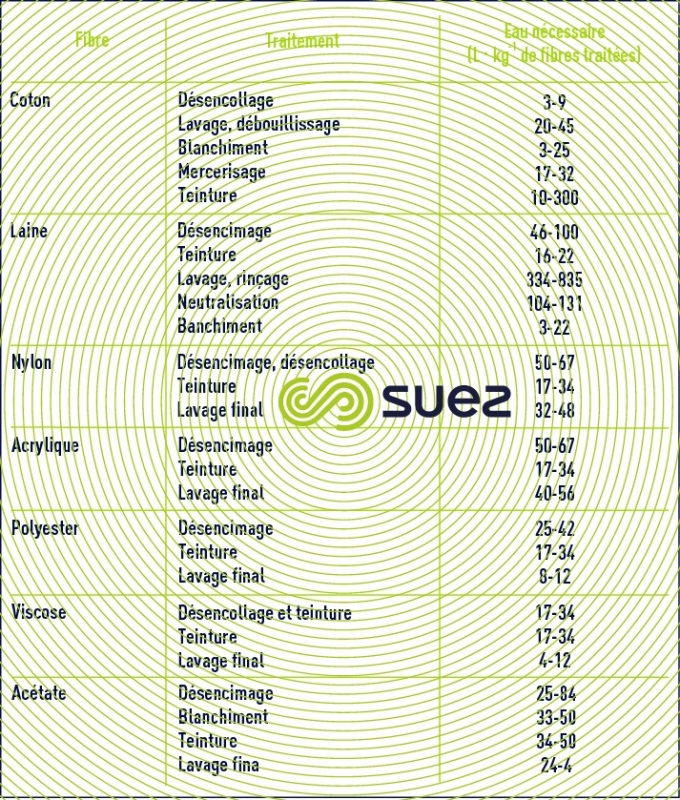

pâtes à papier et papeteries
Ces industries ont de grosses consommations d’eau pour les besoins suivants :
- production de vapeur ;
- préparation des pâtes ;
- fabrication du papier.
consommation d’eau d’appoint
Elles se situaient vers 1975 entre 100 et 300 m3·t–1 de pâte. Depuis, grâce à une politique sévère de contrôle des rejets et donc de recyclage intense, elles ont été considérablement réduites, tableau 23, les circulations spécifiques par atelier restant elles-mêmes élevées.

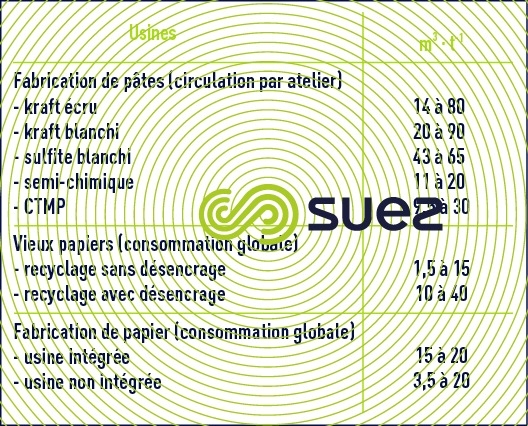

qualité des eaux
Les papeteries cherchent essentiellement à éliminer la turbidité et la couleur des eaux brutes ainsi que leur dureté temporaire.
Des recommandations américaines (National Council of the Paper Industry) préconisent aussi certaines caractéristiques suivant les types de papier (tableau 24).

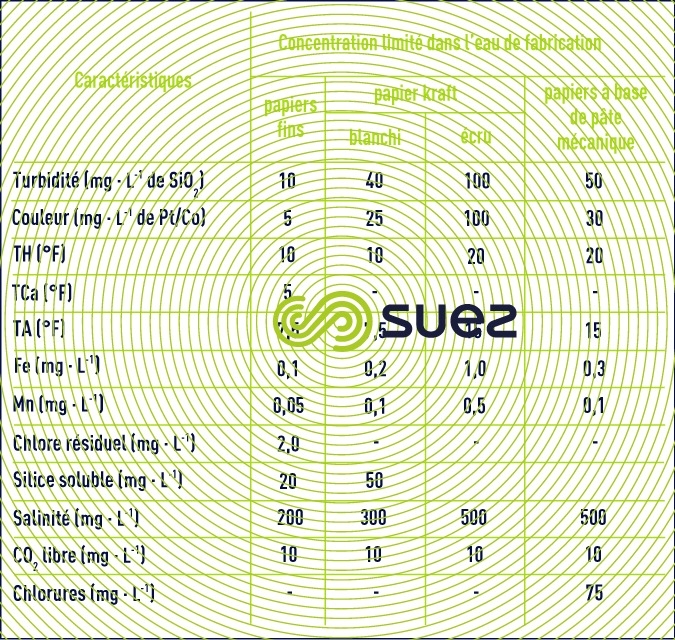

industries du pétrole
eau ou vapeur pour injection dans les formations pétrolières (récupération assistée du pétrole)
Afin de maintenir la pression dans la formation d’où est extrait le brut, ou dans le cas des bruts très vis-queux afin de faciliter leur récupération en les fluidifiant, il est devenu classique d’injecter dans les gisements en cours d’exploitation, soit de l’eau : eau douce, eau de mer en offshore, eau de forage produite avec le brut recyclée, soit de la vapeur (apport calorifique). On récupère en sortie du puits de production un mélange de brut et d’eau produite qui pourra après traitement être recyclée comme eau d’injection.
Suivant les champs, il faut injecter de 2 à 5 fois le débit de brut récupéré et jusqu’à 10 fois le débit de brut récupéré dans le cas des champs matures.
Suivant les champs, on peut injecter jusqu’à 5 ou 6 fois le débit de brut récupéré.
Ces eaux doivent :
- ne pas contribuer au colmatage physique de la formation autour du puits d’injection ; suivant la porosité (perméabilité) de celle-ci on devra donc éliminer les huiles des eaux produites et réinjectées (< 10 ppm, voire < 2 ppm ) et toute particule d’une taille supérieure à une limite donnée (ex. élimination des particules > 2 μ… ou du moins de plus de 98 % des particules > 2 μ) ;
- être « compatibles », c’est-à-dire ne pas être susceptibles de réagir lors de leur mélange avec les eaux de la formation en créant des précipités insolubles. Par exemple en évitant d’injecter de l’eau de mer (forte concentration en SO42–) dans une eau de formation riche en Sr2+ ou Ba2+ ou alors de traiter cette eau de mer en nanofiltration pour éliminer l’essentiel de ces sulfates ;
- ne pas introduire dans la formation de micro-organisme susceptible de développement (ex. bactéries sulfatoréductrices) ce qui impose souvent l’utilisation de biocides.
Dans le cas des injections de vapeur (60-120 bar) celle-ci est produite à partir d’eau douce locale ou d’eau de formation recyclée, ce qui oblige au minimum et suivant le type de chaudière utilisée :
- à une déminéralisation totale (via osmose inverse et échange d’ions) pour les chaudières classiques ;
- à au moins un désiliciage et un adoucissement total (en général < 0,05 °F de TH) pour les chaudières à très fort primage (environ 20 % d’entraînement) souvent utilisées dans cette application.
Dans le cas de la récupération assistée par voie chimique (Chemical Enhanced Oil Recovery), alcalins, polymères ou tensioactifs, leurs propriétés permettent d’améliorer l’extraction du brut, mais nécessitent une qualité d’eau d’injection adaptée, en particulier à faible teneur en ions divalents, généralement sans sulfates et adoucie au moins en partie.
De même, pour l’injection d’eau de faible salinité (TDS/salinité < 5 000 ppm ), une étape supplémentaire d’élimination des ions monovalent par osmose inverse est nécessaire, en remplacement ou en complément de la nanofiltration.
Les hydrocarbures non conventionnels sont extraits après injection de vapeur pour les huiles lourdes et extra-lourdes, par exploitation minière ou en carrière pour les sables et schistes bitumeux, par fracturation hydraulique dans le cas du pétrole et gaz de réservoirs compacts, et du pétrole et gaz de schiste.
La fracturation hydraulique consiste à forer un puit d’extraction horizontal dans la roche-mère contenant les hydrocarbures non conventionnels. Le fluide de fracturation, composé d’un mélange d’eau, de sable (proppant) et d’autres additifs (lubrifiant, biocide), est injecté sous pression. Le long du puits horizontal, de nombreuses fracturesse creusent alors dans la roche mère dans laquelle sont piégés les hydrocarbures. Le mélange du fluide de fracturation et d’hydrocarbures est extrait par pompage par le même puits et séparé. Le fluide de fracturation extrait du puits -ou eau de reflux- contient de nombreux éléments dissous ou en suspension dont il s’est chargé lors du processus de fracturation et doit être traité avant d’être réutilisé comme fluide de fracturation ou même rejeté.
On estime le volume d’eau nécessaire au forage et à la fracturation de 10 000 à 25 000 m3 d’eau par puits, ceci dépendant de la typologie du puits.
De l’eau douce ou saumâtre est utilisée comme fluide de fracturation après élimination des matières en suspension, et après désinfection.
L’eau de reflux doit être traitée après pour élimination des huiles, des matières en suspension et des composés dissous.
eau en raffinage et pétrochimie
Les besoins en eau d’une raffinerie sont importants et indispensables au fonctionnement des unités de raffinage.
La source d’eau peut être de l’eau de surface, de l’eau d’une nappe souterraine, voire partiellement de l’eau de mer.
Les besoins en eau d’appoint proviennent des unités suivantes :
- les chaudières servant à générer la vapeur, indispensable à de nombreuses unités mais dont une partie est souvent perdue ;
- les circuits de refroidissement, principaux consommateurs d’eau et représentent en moyenne plus de 50% de l’eau consommée en raffinerie s’ils sont semi-fermés (taux de concentration élevés), voire même plus de 90% si circuits ouverts
- le dessaleur ;
- certaines unités de cracking et de process de raffinage ;
- les diverses eaux de services (lavage, sanitaires…) ;
- les circuits incendies.
Les qualités nécessaires sont très variables et dépendent des différentes unités (figure 19).

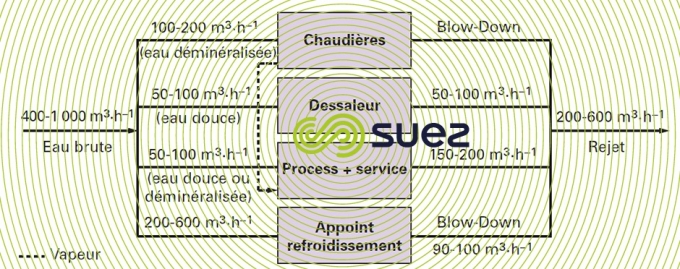

Il est supposé pour la figure 19 que les circuits de refroidissement sont semi-ouverts.
En cas de circuits ouverts (cas des refroidissements par eau de mer), les débits sont très supérieurs.
La mise en place de recyclages au sein de la raffinerie permet d’économiser de l’eau douce et minimise les débits rejetés. Par exemple, les dessaleurs de brut de la distillation atmosphérique sont souvent alimentés par des eaux réutilisées comme les condensats acides des unités de cracking, après stripping de l’ammoniac et de l’H2S. Ou encore, le rejet traité peut alimenter les dessaleurs de brut ou servir d’eau d’appoint pour le refroidissement.
sidérurgie
Grosse consommatrice d’eau, cette industrie a depuis longtemps réalisé des circuits semi-ouverts adaptés aux conditions de travail spécifiques rencontrées.
Il faut distinguer deux grandes utilisations de l’eau dans cette industrie :
- le refroidissement indirect par des échangeurs souvent soumis à des températures de l’eau élevées. Les eaux d’appoint selon les cas seront décarbonatées ou déminéralisées. Ces circuits peuvent aussi être fermés ;
- le refroidissement direct, soit en lavage de gaz, soit en granulation de produits ou en décalaminage, dans lesquels l’eau se salit et doit être constamment traitée dans le circuit.
L’eau d’appoint sera de l’eau décarbonatée ou de l’eau brute.
cokerie
Condensation primaire indirecte des gaz ou finale directe.
Dépoussiérage humide des gaz à l’enfournement du charbon préchauffé et au défournement du coke.
hauts fourneaux
Refroidissement des organes de hauts fourneaux tels que tuyères, tympes, vannes à vent chaud, corps des hauts fourneaux.
Lavage des gaz de hauts fourneaux.
réduction directe
Ce procédé est très gros consommateur d’eau :
- lavage et refroidissement des gaz de réduction des éponges de fer. Les volumes d’eau mis en œuvre (5 à 15 m3·t–1 d’éponge) sont plus élevés qu’en hauts fourneaux et, en raison de la température élevée des gaz, ces eaux sortent très chaudes des laveurs (50 à 70 °C) ;
- refroidissement de la machinerie (compresseurs et réfrigérants à huile).
Une consommation notable d’eau déminéralisée est requise pour la production de vapeur de reformage du gaz de procédé.
convertisseurs
Ces procédés nécessitent des circuits importants :
- refroidissement de la hotte et de la lance (quelquefois assuré par vaporisation) ;
- lavage du gaz avec récupération de calories par combustion partielle du gaz et vaporisation en chaudière BP.
fours électriques et métallurgie en poche
La production d’aciers fins est réalisée dans des fours électriques à arc ou en poches, réchauffées par induction ou par arc ; elle peut être complétée par un dégazage sous vide de l’acier. L’eau intervient de trois façons :
- refroidissement normal des fours et des poches ;
- production de vapeur pour les éjecteurs de mise sous vide ;
- refroidissement des lingotières et des électrodes à partir d’eau déminéralisée.
coulées continues de brames et billettes
Trois circuits sont usuels :
- refroidissement de la lingotière en circuit fermé avec appoint d’eau déminéralisée ou eau - adoucie ;
- refroidissement de la machine, en circuit semi-ouvert, avec conditionnement adapté ;
- aspersion de la machine et de la brame ou des billettes, avec production de battitures de décalaminage et de laitier d’oxycoupage.
trains de laminage à chaud
ll faut alimenter deux types de circuits :
- refroidissement indirect de fours, compresseurs, moteurs… ;
- refroidissement direct pouvant assurer trois fonctions : refroidissement du métal et des cages de laminage, décalaminage de l’acier.
Les trains « à chaud » sont très variés :
- Trains à bandes
Les plus importants traitent 300 à 1 000 t·h–1 d’acier sous forme de brames.
Débits de circulation mis en jeu :
- refroidissement direct : 10 à 25 000 m3·h–1 ;
- refroidissement indirect : 5à 10 000 m3·h–1.
Des circuits de refroidissement séparés équipent les moteurs, les cuves à huile et les fours de réchauffage.
Ils sont souvent complétés par :
- l’écriquage automatique, générateur de grandes quantités de laitier granulé ;
- le refroidissement de brames, en piscine, en tunnel ou sous aspersion, qui met en œuvre de grands débits, sans créer de fortes pollutions.
- Autres trains à chaud
- trains à tôles plates ou trains quartos;
- blooming-slabbing ;
- trains à profilés, à poutrelles, à fers marchands ;
- trains à ronds ou à fil ;
- laminoirs de tubes.
laminoirs à froid
L’élaboration de produits laminés de faible épaisseur, galvanisé étamé ou non, nécessite des prétraitements du métal tels que le dégraissage et surtout le décapage. Ce dernier est réalisé de plus en plus fréquemment à l’acide chlorhydrique régénéré in situ.
L’alimentation des rinçages finaux des ateliers de zingage ou d’étamage requiert de l’eau déminéralisée. Une eau très pure et adoucie est également requise pour la préparation des bains d’huiles solubles.
métallurgie du cuivre
L’élaboration du métal peut se faire par voie sèche ou par voie humide suivant la nature des minerais. Les procédés hydrométallurgiques, utilisant une lixiviation à l’acide sulfurique et une électrolyse, sont de plus en plus fréquents, car ils permettent de traiter les minerais pauvres, voire les résidus anciens de flottation.
Le laminage du cuivre, à partir des « wirebars », assure la production de profilés, de câbles ou de fils.
Les opérations de dégrossissage mettent en œuvre un décalaminage hydraulique de la surface du métal et provoquent la mise en suspension dans l’eau d’oxydes de cuivre, produits valorisables souvent intéressants à récupérer. Par ailleurs, les conditions d’exploitation des circuits de décalaminage et de refroidissement sont analogues à celles de la sidérurgie.
hydrométallurgie
Cette industrie concerne en particulier l’extraction de l’uranium, de l’or, du cobalt… et utilise les procédés élémentaires suivants :
- extraction du métal par attaque acide ou alcaline (lixiviation) ;
- séparation solide/liquide : filtration et/ou décantation ;
- concentration des métaux : extraction par solvants ou par échangeurs d’ions ;
- précipitations diverses.
Ces procédés ont pour avantage d’être effectués à froid et minimisent les problèmes de corrosion. Les technologies employées sont souvent proches de celles du traitement des eaux et peuvent ainsi bénéficier de l’expérience acquise dans notre domaine. Les paramètres les plus significatifs, en particulier pour la clarification des liqueurs, sont :
- MES: après décantation, les liqueurs contiennent encore fréquemment 100 à 200 mg·L–1 de MES, parfois plusieurs g·L–1. Ces matières résiduelles sont gênantes aussi bien dans le cas d’une extraction directe du métal que dans celui d’une purification-concentration par solvant organique ou par résines. Beaucoup d’utilisateurs souhaitent en réduire la teneur à moins de 10 à 20 mg·L–1 ;
- silice colloïdale: la silice est présente dans les liqueurs sous forme ionisée (acide silicique ou acide fluo silicique) à des concentrations maximales possibles de 200 à 500 mg·L–1 ou sous forme de gel d’acide polysilicique peu ionisé. Cette dispersion colloïdale est électropositive, donc non coagulable par les techniques usuelles. Cette silice peut précipiter sur les résines ou en présence de solvants ;
- sulfate de calcium: les minerais calcaires et dolomitiques traités par l’acide sulfurique donnent naissance à des liqueurs sursaturées en CaSO4 cause d’entartrage et de précipitation. On doit briser les sursaturations par ensemencement de microcristaux de gypse avant tout autre traitement ;
- matières organiques : elles sont nuisibles dans deux cas :
- en extraction liquide-liquide, le solvant résiduel nuit à la précipitation du métal, surtout en électrolyse ;
- en fixation sur charbon ; certaines matières organiques adsorbées peuvent ne pas être éluées à la régénération chimique. D’autres forment avec le métal un complexe non adsorbable.
les industries automobile et aéronautique
L’industrie automobile comprend des usines mécaniques : construction de moteurs et de boîtes de vitesse, des usines de carrosserie et de montage, et de nombreux ateliers de sous-traitance indépendants. Les besoins en eau d’appoint sont donc très différents suivant les situations.
Néanmoins, trois familles peuvent être distinguées :
- refroidissement, principalement de compresseurs et de conditionneurs d’air ;
- préparation de bains divers d’électroplastie et de peintures nécessitant en général de l’eau déminéralisée ;
- alimentation des centrales d’usinage et rectification en eau peu minéralisée ou adoucie.
L’industrie aéronautique présente des besoins similaires.
industries électroniques
C’est le domaine où les qualités les plus extrêmes sont requises. L’essentiel de ces eaux sert au rinçage des « tranches de silicium » après chacune des opérations élémentaires d’implantation des composants et circuits.
Le tableau 25 illustre l’évolution des spécifications des eaux de rinçage des mémoires DRAM où la finesse de plus en plus grande de gravure impose de ne laisser, via ces eaux, ni dépôt particulaire, ni bactérie (même morte), ni sels qui puissent créer un défaut de taille significative.
Remarque : chaque fabricant, suivant le type de mémoire, de circuit intégré… qu’il fabrique, a des exigences particulières mais dans tous les cas, la course à la miniaturisation conduit à ces exigences extrêmes qu’il faut en sus obtenir avec un grand degré de fiabilité (voir chapitre traitement et conditionnement des eaux industrielles). Tout défaut de qualité se traduit par une augmentation des taux de rebut des produits fabriqués pouvant aller jusqu’à nécessiter un arrêt de production et des pertes financières considérables.

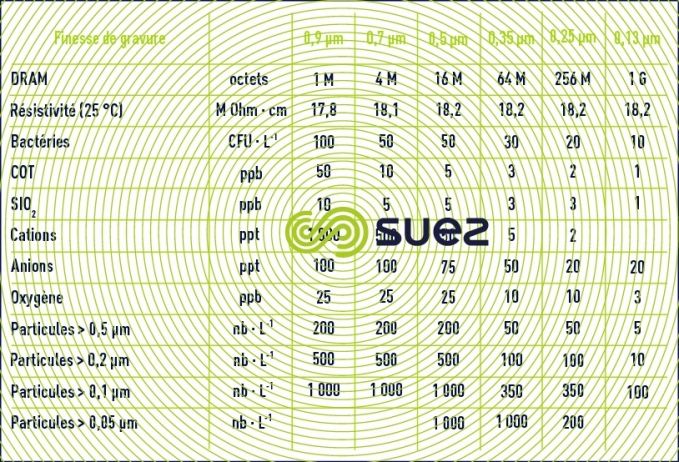

industries pharmaceutiques et biotechnologiques
Ces deux domaines demandent des qualités d’eau extrêmement poussées :
- les eaux incorporées dans les médicaments eux-mêmes et en particulier celles des solutions injectables ; celles-ci sont soumises aux différentes normes nationales (Codex) (voir eaux ultrapures pour les industries des semi-conducteurs et de la pharmacie) et doivent en particulier être exemptes de :
- toutes les bactéries
- tous virus ;
- mais également être apyrogènes (ne doivent pas provoquer de fièvre lors de leur injection) ce qui implique par exemple l’absence d’anticorps ou de tout ou partie des matériaux membranaires ou intracellulaires des bactéries tuées lors des stérilisations ;
La pharmacopée européenne distingue trois qualités d’eau : eau purifiée ( EP ), eau hautement purifiée ( EHP ) et eau pour préparations injectables ( EPPI ). Leurs spécifications sont comparées dans le tableau 26.
La pharmacopée américaine ne distingue pas l’eau hautement purifée de l’eau purifiée. Quelques recommandations données par la pharmcopée USP 34 sont mentionnées dans le tableau 27.
- les eaux utilisées pour la multiplication de certaines souches bactériennes ou levures…, dont on extrait ensuite des principes actifs.
Dans les deux cas, les chaînes doivent être adaptées aux spécifications précises des industriels, néanmoins, comme pour l’industrie électronique, les combinaisons de membranes s’imposent pour pouvoir garantir qualité et fiabilité (voir eaux ultrapures pour les industries des semi-conducteurs et de la pharmacie).

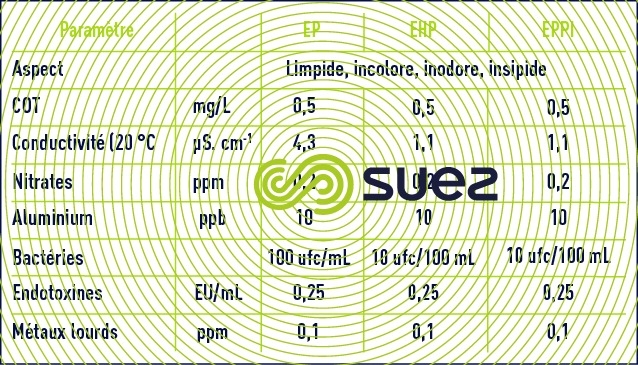


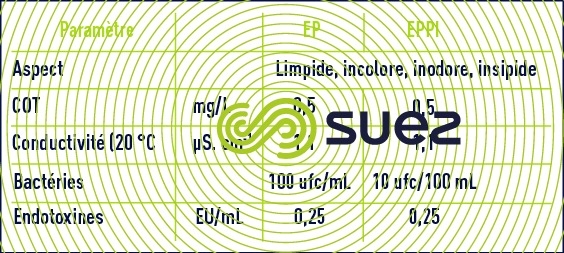

Outil Marque-page
Cliquez sur l'outil marque-page, puis surlignez le dernier paragraphe lu pour pouvoir poursuivre ultérieurement votre lecture.
