l'incinération dédiée en lit fluidisé: four thermylis-htfb degremont®
Temps de lecture :le dimensionnement
Les données de base nécessaires à l’établissement d’un bilan thermique d’un four sont :
- le débit massique des boues à traiter exprimé en kg · h–1 ;
- la siccité des boues à traiter (%) ;
- le taux des matières organiques (%) ;
- le PCI des matières organiques (kJ · kg–1 de MO) ; si celui-ci n’est pas connu, on peut avoir recours au calcul pour autant que l’on connaisse l’analyse élémentaire des matières organiques (C, H, O, N, S) – par exemple la formule de Dulong-Petit :
PCS = 81,3 C + 345,5 (H-O/8) + 22,2 S et PCI = PCS – 54 H.
Les critères principaux (physiques ou réglementaires) à intégrer dans le calcul du bilan thermique sont :
- température dans le lit : minimum de 800 °C ;
- température au sommet du freeboard : 850 °C ;
- temps de rétention dans le freeboard : minimum 5 s ;
- vitesse de fluidisation à la grille : 0,9 m · s–1 ;
- vitesse de fluidisation au sommet du lit : 0,85 m · s–1 ;
- vitesse des produits de combustion au sommet du freeboard : 0,65 m · s–1 ;
- hauteur du lit de sable en expansion : 1,5 m environ ;
- teneur en O2 dans les fumées ≥ : 6 % sur gaz sec ;
- température de l’air de fluidisation qui ne peut pas dépasser 650 °C dans la boîte à vent.
Sur ces bases, on établit un bilan thermique qui détermine en priorité :
- le débit d’air nécessaire pour oxyder les matières organiques alimentées (incluant un excès de 40 %). Ce débit doit tenir compte de la vitesse de fluidisation requise et des corrections de température et pression au niveau de la grille. Il détermine la section intérieure de celle-ci et, par voie de conséquence, le diamètre intérieur du four au niveau de la grille ;
- l’équilibre thermique, qui est le résultat d’un calcul itératif faisant intervenir la température de l’air de fluidisation, le taux d’oxygène, la température de 850 °C dans le freeboard. Son résultat définit :
- le besoin en combustible d’appoint ;
- la composition des produits de combustion ;
- le profil des températures ;
- les dimensions principales du four ;
- les caractéristiques principales de l’échangeur réchauffant l’air de fluidisation grâce à la chaleur sensible des fumées.
Figure 27. Schéma four à lit fluidisé Thermylis-HTFB

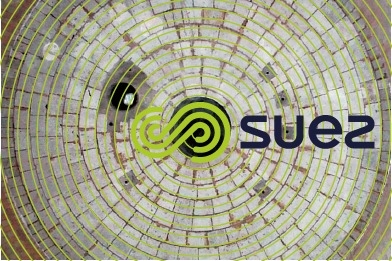


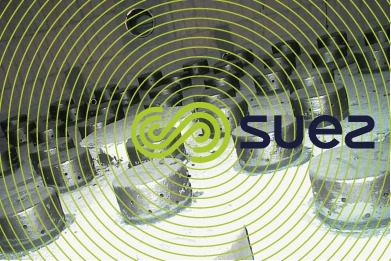

le bilan thermique
Il est effectué par un logiciel spécifique dont les équations principales sont les suivantes :


Avec pour les entrées :
QAB = quantité de chaleur apportée par l’air de balayage (air servant à refroidir les parties exposées à un échauffement important : cannes d’injection d’eau, de combustible auxiliaire, de boues…).
QAF b+g = quantité de chaleur apportée par l’air de fluidisation nécessaire à la combustion de la matière organique (déduction faite de l’air de balayage).
Qs(e) = quantité de chaleur apportée par le débit de sable visant à compenser les pertes par attrition.
Qb+g = quantité de chaleur sensible apportée par les produits alimentés.
Qcomb b+g = quantité de chaleur apportée par la combustion totale de la matière organique.
Qca = quantité de chaleur apportée par la combustion du combustible d’appoint.
QAFca = quantité de chaleur apportée par l’air de fluidisation nécessaire à la combustion du combustible d’appoint (il s’ajoute à l’air de fluidisation).
Avec pour les sorties :
Qcendres = chaleur sensible évacuée par les cendres.
Qgaz sortie b+g = chaleur sensible des fumées issues de la combustion des matières
organiques (y compris excès d’air).
Qgaz sortie ca = chaleur sensible des fumées issues de la combustion du combustible d’appoint.
Qs(s) = chaleur sensible des particules de sable emportées dans les fumées.
Qpertes = chaleur perdue par pertes thermiques.
Le tableau 9 reprend un bilan thermique simplifié appliqué à une boue déshydratée. On constate l’importance du préchauffage de l’air : environ 22 % des calories apportées au four, l’importance de la chaleur latente de l’eau vaporisée (34 %) et de l’excès d’air (9 %) dans les chaleurs perdues.
Remarque : la même boue à 22 % de siccité apporterait 740 L · h–1 d’eau en plus et nécessiterait environ 65 L fuel · h–1 !

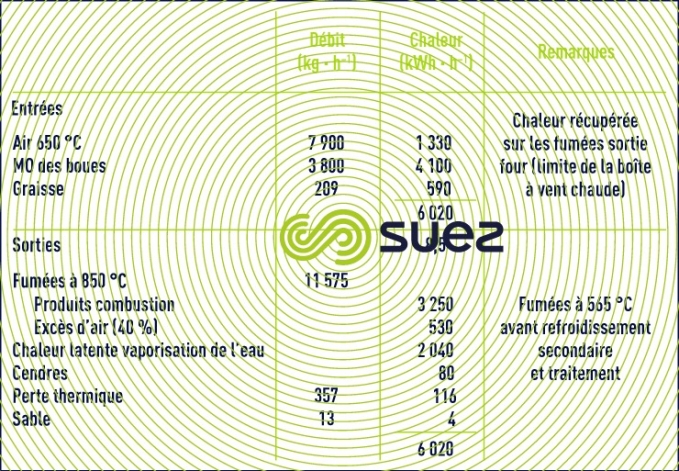

les principes généraux de fonctionnement
Le four à lit fluidisé est fondé sur le principe de la mise en suspension dans un courant d’air chaud préchauffé de particules de sable précalibrées. La figure 28 montre la zone de la fluidisation d’un sable par de l’air (voir fluidisation). Il y a environ un rapport de 1 à 10 entre ut et uo et la courbe caractéristique dépend évidemment de la granulométrie et de la densité du sable constitutif du lit. La physique et la thermodynamique des lits fluidisés ont été largement décrits dans des ouvrages de référence (Fluidisation engineering, Daizo Kunii et Octave Levenspiel, Fluidisation, Max Leva).

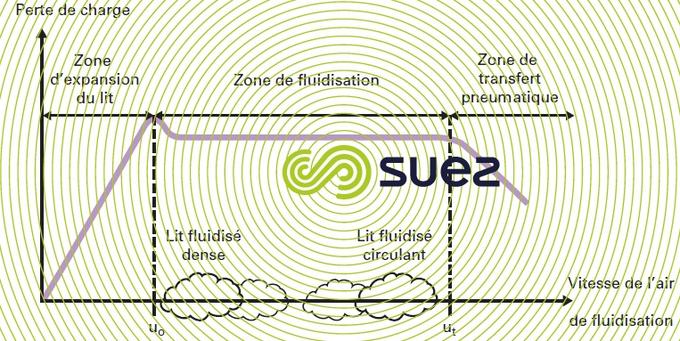

Le four à lit fluidisé Thermylis-HTFB degremont® est du type à lit fluidisé dense sans débordement de lit. Le lit de sable fluidisé porté à la température d’incinération (800‑850 °C) est un milieu extrêmement turbulent dans lequel les échanges de chaleur atteignent des coefficients de transfert très élevés. La boue déshydratée alimentée dans ce lit est très rapidement désintégrée par la turbulence du sable, l’évaporation prend place instantanément ainsi que la combustion de la matière organique avec l’air de fluidisation comme comburant.
Comme il n’y a pas de débordement de lit, la hauteur du lit expansé reste stable (aux pertes de sable près, dues à l’attrition). En effet, la matière minérale de la boue a une granulométrie très faible par rapport aux grains de sable du lit, si bien que la totalité des cendres minérales sont entraînées pneumatiquement dans la zone supérieure du four et ensuite dans les carneaux d’évacuation des fumées (cendres volantes).
le principe de construction du four
Le four est constitué d’une virole métallique, à l’intérieur de laquelle un garnissage réfractaire est maçonné. Il comprend six parties qui s’empilent du bas vers le haut dans un système auto-stable et autoportant.

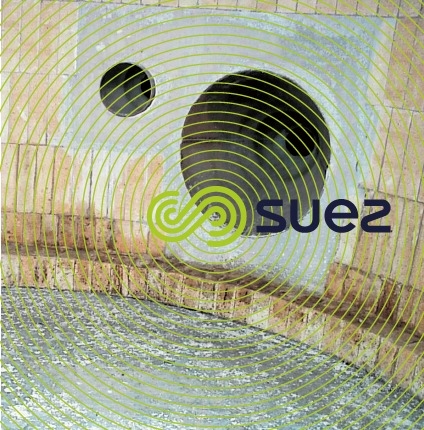

la boîte à vent
De section cylindrique, elle reçoit par une large entrée radiale la gaine d’amenée d’air de fluidisation en provenance de la soufflante. Suivant que cet air arrive préchauffé en deçà d’une température de 250 °C, on parle d’une boîte à vent froide ; au-delà, il s’agit d’une boîte à vent chaude. La plus grande partie des fours à lit fluidisé traitant les boues sont de conception boîte à vent chaude.
Cette boîte à vent est garnie de réfractaire de type silicoalumineux avec un isolant intermédiaire entre la virole et la partie réfractaire proprement dite. La partie supérieure de la boîte à vent supporte le dôme de fluidisation. La boîte à vent est équipée d’un brûleur (éventuellement rétractable) qui sert pour le préchauffage lors des procédures de mise en route (photo 18).
- Le dôme de fluidisation
C’est la pièce essentielle du four car c’est au travers de ce dôme que se fait la répartition de l’air de fluidisation. Dans la version boîte à vent chaude, le dôme est constitué d’un ensemble d’anneaux de briques réfractaires de forme (voir détail photos 16 et 18). Ces anneaux se serrent mutuellement pour former une voûte autoportante. Chacune des briques de forme comporte un trou vertical qui reçoit la tuyère de fluidisation.
Le nombre de tuyères et leur section définissent une surface ouverte qui détermine la perte de charge du dôme de fluidisation. Celle-ci est de l’ordre de 50 à 60 mbar. Dans la version boîte à vent froide, le dôme de fluidisation est constitué d’un « sandwich » formé d’une tôle concave en acier réfractaire sur laquelle sont rapportées par soudure les tuyères de fluidisation. Cette tôle est noyée dans un enrobage en béton réfractaire ;
- Les tuyères de fluidisation
Elles ont, le plus fréquemment, la forme d’un champignon dont la tête est circulaire. La vitesse de l’air dans la tuyère est de l’ordre de 40 m · s–1 ; cette tuyère, en fonte réfractaire scellée dans le trou de la brique réfractaire support, constitue un point clé de la construction du four. Toute perte de tuyère engendre un dysfonctionnement grave car il y a passage direct du sable de fluidisation dans la boîte à vent et perturbation conséquente de la fluidisation.
la zone proprement dite de fluidisation
Elle correspond à la hauteur du lit de sable expansé qui s‘élève dans la plupart des cas entre 1,5 et 2 m. Cette zone est également garnie de réfractaires silicoalumineux avec une partie isolante entre réfractaires et virole métallique. C’est dans cette zone que sont disposées les alimentations en boues et les injections de combustible d’appoint (fuel, gaz, biogaz).
la zone d’expansion
Appelée freeboard, elle est évasée de manière à prendre en compte l’augmentation du volume des produits gazeux due à la fois à la température et à l’achèvement de la combustion et également permet la diminution progressive de la vitesse d’entraînement afin de défluidiser les particules de sable plus fines. Cette zone d’expansion sert également de postcombustion et confère aux produits de combustion un temps de rétention très long (au moins 5 s) ce qui permet, en toutes circonstances, d’être conformes aux normes de l’incinération des déchets. L’appoint en sable de fluidisation afin de compenser les pertes par attrition est fait dans cette zone.
la voûte supérieure
Elle est constituée d’anneaux en briques de forme réfractaires pour constituer une voûte autoportante, elle s’appuie sur l’enveloppe extérieure de la zone d’expansion. Le centre de cette voûte est creux et constitue l’amorce du carneau de sortie des produits de combustion. Dans cette voûte sont disposés des injecteurs d’eau permettant le contrôle des températures (sécurité) ;
le carneau de liaison
Situé entre la sortie du four et l’entrée de l’échangeur de récupération. Ce carneau est également réfractorisé et doit contenir un joint de dilatation.
l’extérieur du four
Il est encadré par un ensemble de passerelles indépendantes de la structure du four. Il faut au moins deux niveaux de passerelles : l’une au niveau des alimentations en boues et combustible d’appoint, l’autre sur le dessus de la voûte, donnant accès au carneau d’évacuation des produits de combustion.
l’optimisation de la consommation d’énergie
la recherche de l’auto-thermicité (figure 29)
L’optimisation de la consommation d’énergie est un point essentiel de la conception d’un atelier d’incinération dédiée : la recherche de l’auto-thermicité est systématiquement effectuée en recherchant la valorisation optimale de la chaleur sensible des produits de combustion. C’est un compromis entre la minimisation de la consommation de fuel d’appoint et celle des coûts d’investissement et d’exploitation.

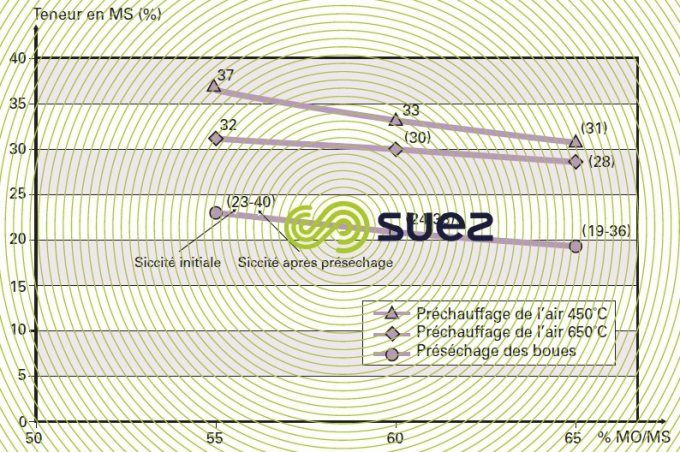

Trois cas de figures se dégagent :
cas 1 (figure 30)
Le préchauffage de l’air de fluidisation par une récupération partielle de la chaleur sensible des fumées suffit. Cependant, le seuil de température de 650 °C est le maximum que l’on puisse raisonnablement atteindre.
cas 2 (figure 31)
Il faut récupérer le maximum d’énergie contenue dans la chaleur sensible des fumées. Dans ce cas il faut passer par une chaudière de récupération associée à un sécheur. De la sorte, une partie importante de l’eau contenue dans les boues n’est ni évaporée ni surchauffée dans le four.

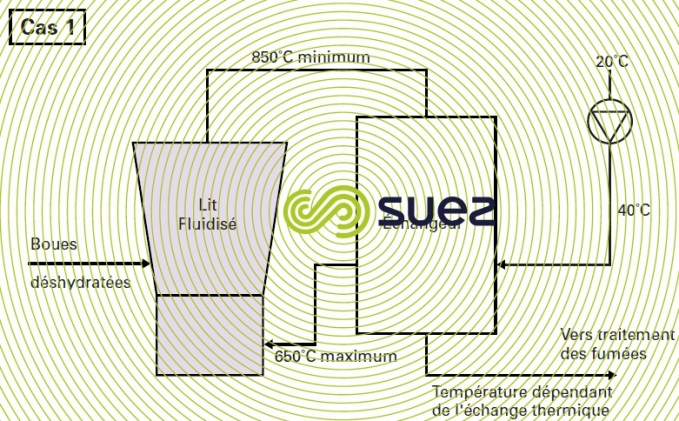


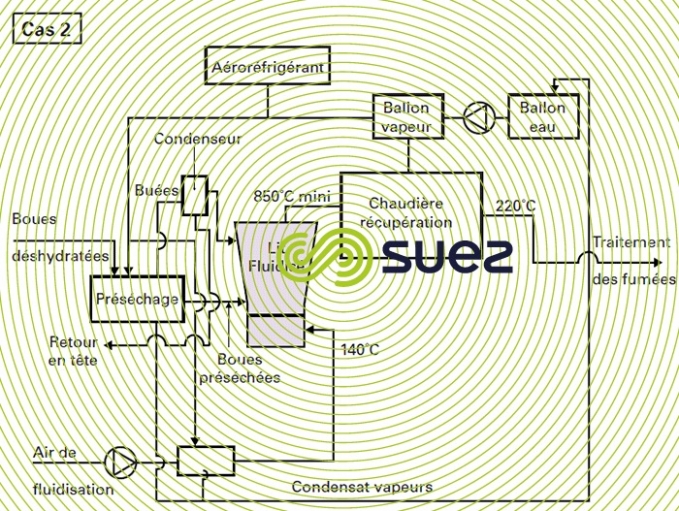

cas 3 (figure 32)
C’est également une récupération complète de la chaleur sensible des produits de combustion mais dans un système mixte. Comme le cas 1, on installe un échangeur pour le préchauffage de l’air de fluidisation et, ensuite, on installe une chaudière à huile thermique générant de l’huile à environ 200 °C et qui assure également un séchage partiel de la boue. Dans cette configuration, le tableau 9 lignes 1 et 2 montrent l’impact important de la teneur en eau de la boue d’alimentation : dans l’exemple retenu, un pré-séchage très partiel (26 → 34 % MS) permet de gagner 5 700 m3 · h–1 de fumées (vapeur d’eau), soit 25 % de celles-ci, et d’être légèrement excédentaire en énergie au lieu de devoir fournir 2,7 MWh · h–1 sous forme de fuel d’appoint.

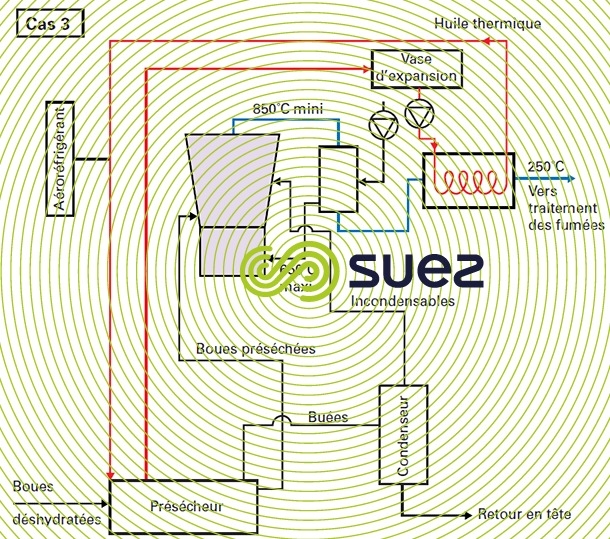

On évite dans cette conception le passage par la chaudière vapeur qui comporte des contraintes lourdes de construction et d’exploitation. La chaudière à huile thermique peut être éventuellement remplacée par une chaudière à eau surpressée.

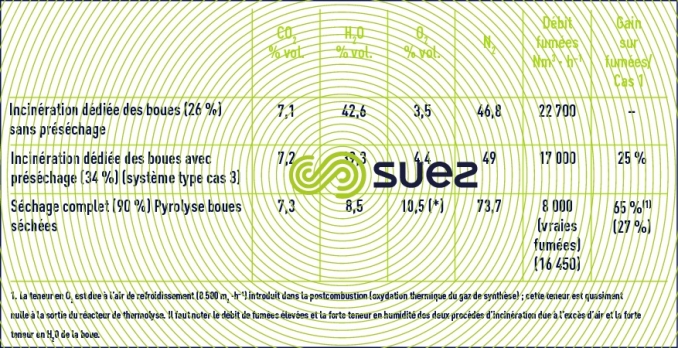

Chacun des trois cas précités présente des avantages et inconvénients qu’il faut prendre en compte avant de faire un choix et de passer à l’ingénierie d’exécution d’un projet. Le tableau 11 résume de façon générale les avantages et inconvénients majeurs de chacune de ces solutions.
les technologies appliquées aux procédés de récupération d’énergie :
échangeur de préchauffage de l’air de fluidisation
Échangeurs exclusivement convectifs multipasses à tubes croisés : l’air de fluidisation passe dans les faisceaux tubulaires et les fumées dans la calandre de l’échangeur.
Ces échangeurs ont été systématiquement utilisés dans le passé et ont donné lieu à des soucis d’exploitation provoqués par des pertes d’étanchéité au passage des tubes dans la calandre des échangeurs. Ces échangeurs sont sensibles à la charge en poussières, particulièrement le bloc de tête où des phénomènes d’incrustation peuvent survenir, surtout en cas de surchauffe des fumées les rendant proches de la température de ramollissement des cendres (influencée par la teneur en P).
Échangeurs exclusivement à tubes de fumées : c’est le fonctionnement inverse du précédent : les fumées parcourent les tubes alors que l’air est dans la calandre de l’échangeur. Ils sont de construction plus simple et plus compacte. Il faut cependant s’assurer de la conception des joints de dilatation sur les tubes de fumées et du non encrassement de ceux-ci par les cendres. Les tubes de fumées doivent pouvoir être nettoyés lors des interventions de gros entretien.
Échangeurs radiants/convectifs : ces échangeurs ont une double paroi qui est utilisée comme partie radiante. Les fumées passent d’abord dans cette partie radiante où elles cèdent une partie de leur chaleur sensible ; de la sorte, le faisceau tubulaire convectif est moins sollicité thermiquement.
Échangeurs radiants à tubes de fumées : même principe que ci-dessus avec l’application des tubes de fumées.
Dans nos applications les plus courantes (cas n° 1), nous recommandons l’usage des échangeurs à tubes de fumées.

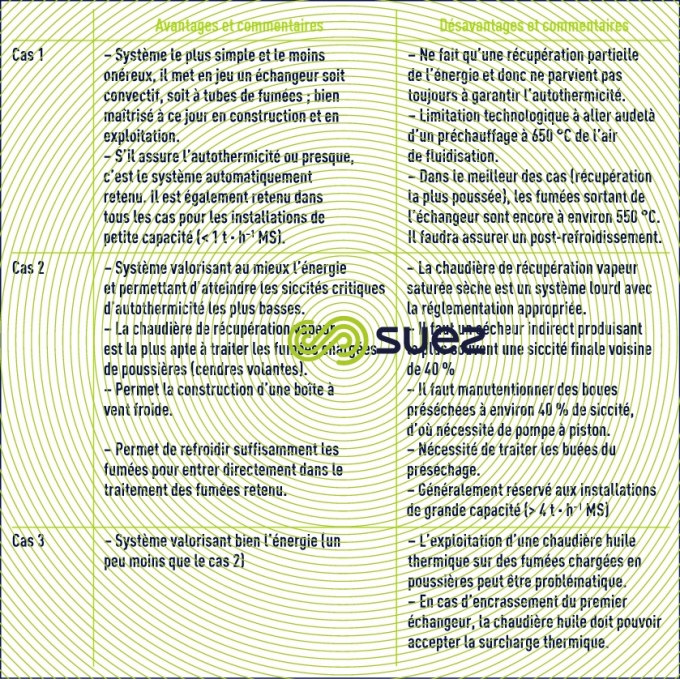

chaudière de récupération vapeur
Contrairement aux applications chaudières dans les unités de traitement des ordures ménagères (vapeur surchauffée avec turbine pour production d’électricité), il s’agit d’une simple chaudière à circulation naturelle et produisant de la vapeur saturée sèche. Cette installation doit comprendre un aéroréfrigérant pour dissiper la vapeur produite en excès éventuel et systématiquement durant les opérations de chauffe lorsque l’alimentation du four en boue pré-séchée n’est pas démarrée. En effet il n’est pas possible de stocker et déstocker des boues pré-séchées dans une large zone de siccité (35 à 65 %).
chaudière huile thermique
Ce sont des échangeurs classiques à épingles qui doivent éventuellement être protégés en amont par un dépoussiérage partiel (cyclonage par exemple).
l’exploitation
Le four à lit fluidisé a une faible flexibilité quant aux variations de débit de boues, à bilan thermique constant (flexibilité d’environ 15 % par rapport à la charge nominale).
En revanche, il est très flexible en exploitation. Il peut supporter des arrêts et démarrages fréquents permettant notamment d’envisager un mode d’exploitation où l’incinération est mise en veilleuse durant les postes de nuit et le week-end.
Un certain nombre d’automatismes sont nécessaires pour contrôler le procédé ; en particulier la qualité de la combustion est contrôlée par un algorithme de régulation et ne nécessite donc pas de présence permanente en salle de contrôle. Toutefois, une présence humaine « à proximité » est toujours nécessaire pour assurer une intervention rapide en cas de dysfonctionnement (par exemple : panne d’électricité).
Outil Marque-page
Cliquez sur l'outil marque-page, puis surlignez le dernier paragraphe lu pour pouvoir poursuivre ultérieurement votre lecture.
