cuivre
Temps de lecture :Sur les sites d’extraction, le minerai est habituellement préconcentré par flottation avec ajouts de produits chimiques, le traitement des purges et rejets de cet atelier est effectué sur le site de la mine (voir industries minières), les concentrés sont ensuite traités pour en extraire le métal selon deux techniques.
pyrométallurgie
Cette technique est peu consommatrice d’eau, il s’agit essentiellement de refroidissements et également de traitement des gaz et fumées très chargés en SO2 qui est généralement associé à une production d’acide sulfurique.
Le cuivre est préparé par grillage, fusion et coulée. Le lingot de métal obtenu est mis à l’anode d’un raffinage électrolytique (electrorefining) pour obtenir à la cathode un cuivre très pur. (consommation environ 250 kWh · t–1 Cu). Il y a peu de rejet sur ce poste, essentiellement des résidus d’électrolyse, boues de fond et nettoyages de sols.
hydrométallurgie
Elle traite en tas les minerais préconcentrés par lixiviation acide ou acide/oxydante. La solution est récupérée soit directement, soit par lavage/décantation en cascade.
La purification/concentration s’effectue, la plupart du temps, par précipitation sélective des impuretés. À ce stade, les impuretés valorisables sont récupérées.
On peut rencontrer également des purifications par extraction liquide-liquide.
La production s’effectue ensuite par electrowinning : électrolyse d’extraction du cuivre comportant une anode inerte (Pb ou Ti) et une cathode en cuivre pur. Ce procédé consomme 2 500 à 3 000 kWh · t–1 de cuivre produite.
Le cuivre se dépose à la cathode et les gaz produits à l’anode (O2, Cℓ2) sont récupérés sélectivement et renvoyés vers le process.
Cette méthode donne un cuivre très pur qui peut être alors laminé (à chaud et à froid), tréfilé ou encore mis en forme de tube avant sa commercialisation.
Dans ces usines, le traitement des effluents est important. Il concerne :
- les pluviales récupérées des toitures, des zones pavées et des tas de stériles ;
- les lavages de gaz acide contenant beaucoup de SO2 ;
- les effluents résiduels de lixiviation très acides ;
- les effluents résiduaires industriels de l’usine (granulation, décapages divers, résidus d’électrolyse…).
Leurs traitements sont de plusieurs sortes (figure 60), les lavages de gaz sont traités par l’usine avec une production d’acide sulfurique intéressante pour la lixiviation. Les effluents acides sont neutralisés à la chaux afin de précipiter le gypse (éventuellement valorisable) et décantés de façon classique. Les effluents résiduaires et les pluviales sont aussi traités par neutralisation à la chaux. Ils reçoivent également la surverse des décanteurs du traitement des acides. Le tout est à nouveau décanté à pH optimum pour éliminer les métaux lourds divers, dans un décanteur à densification de boues comme le Densadeg.
Une filtration finale peut être nécessaire pour éliminer MES et traces de métaux avec ajout d’un insolubilisant polymère.
Le recyclage de cet effluent est tout à fait possible (25 à 30 %) vers des utilisations peu nobles dans l’usine, un traitement tertiaire plus poussé peut être installé pour un recyclage plus important vers le process.

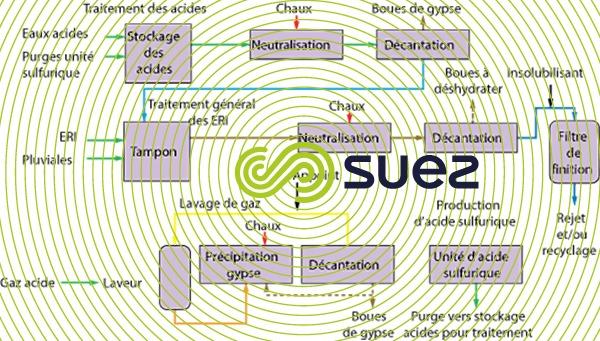

Outil Marque-page
Cliquez sur l'outil marque-page, puis surlignez le dernier paragraphe lu pour pouvoir poursuivre ultérieurement votre lecture.
