filtration sur lit granulaire
Temps de lecture :La technologie des différents filtres est décrite à la section les filtres ; le présent § est limité aux paramètres influençant la filtration.
L’eau à filtrer percole à travers un lit filtrant constitué d’un ou plusieurs matériau(x) granulaire(s), dont les caractéristiques et la hauteur de couche doivent être adaptées à l’eau à traiter et au type de filtre choisi. Les matières en suspension sont retenues dans les espaces intergranulaires, sur la plus grande partie de la hauteur de couche.
les milieux poreux
caractéristiques physiques
Un matériau est caractérisé par différents paramètres dont les protocoles de mesure sont détaillés à la section examen des matériaux granulaires et pulvérulents :
- la granulométrie définie par le couple : taille effective (TE) et coefficient d’uniformité (CU) ;
- la forme des grains : anguleux (matériau concassé), ou ronds (sable de rivière ou de mer), ou plus ou moins plats (voir mesure du coefficient d’aplatissement). Cette forme des grains est importante : ainsi, on obtient des qualités d’eau filtrée semblables avec un matériau anguleux de taille effective plus faible que celle d’un matériau à grains ronds, ou bien, à granulométrie égale, l’accroissement de perte de charge est plus faible avec des grains anguleux qu’avec des grains ronds ; en effet, la porosité d’un lit à grains anguleux est plus élevée car contrairement à ce que l’on peut penser, les grains de ce type s’imbriquent moins facilement les uns dans les autres que les grains ronds, et laissent des sections de passage plus grandes ;
- la friabilité qui permet de choisir les matériaux susceptibles d’être utilisés en filtration, sans risque de production de fines par les opérations de lavage. Un matériau trop friable est à proscrire, surtout dans un filtre fonctionnant de haut en bas et dont le lavage se termine par une phase d’expansion à l’eau seule car les fines formées s’accumulent en surface et y bloquent l’encrassement ;
- la perte à l’acide : il est bien évident qu’on ne peut tolérer une perte à l’acide importante quand l’eau est susceptible de contenir du gaz carbonique agressif ou toute acidité minérale;
- la masse volumique des grains constituant le milieu filtrant en relation avec leurs vitesses minimales de fluidisation ;
- les masses volumiquesapparentes (en vrac) dansl’air et dans l’eau.
D’autres caractéristiques sont spécifiques des matériaux adsorbants comme le charbon actif ; elles sont également examinées à la section examen des matériaux granulaires et pulvérulents.
nature du milieu poreux
Le sable quartzeux a été le premier des matériaux utilisés pour la filtration et c’est encore le matériau de base pour la plupart des filtres actuels.
Certains filtres utilisent une combinaison de plusieurs matériaux (filtres multicouches). Le sable peut alors être associé à de l’anthracite, de la pierre ponce, du grenat, des schistes plus ou moins poreux…, à condition que la friabilité de ces matériaux soit faible ainsi que leur perte à l’acide.
La filtration peut s’effectuer sur du charbon actif granulé, suffisamment résistant : en premier étage de filtration quand on veut à la fois éliminer le floc résiduel et lutter par adsorption contre une pollution ; ou mieux en second étage de filtration pour un traitement d’affinage seul ou de déchloration.
Pour certains traitements où l’on cherche à favoriser une action biologique, il est intéressant d’utiliser des matériaux à forte surface spécifique, tels que les biolite, schistes expansés, pouzzolanes…
L’anthracite ou le marbre peuvent être substitués au sable quand il est nécessaire d’éviter toute trace de silice dans certains traitements industriels (traitement des condensats par exemple) ou quand leur approvisionnement est plus facile (et pour le marbre, quand l’eau ne présente aucune agressivité).
contrôle et optimisation
suivi d’un cycle de filtration
Le fonctionnement du filtre est généralement suivi à l’aide de trois moyens de contrôles.
mesure et évolution de la qualité de leau filtrée
La courbe b de la figure 39 donne l’évolution de la turbidité du filtrat et définit les périodes caractéristiques de fonctionnement du filtre :
c = période de maturation,
b = période de fonctionnement normal,
d = début de crevaison du filtre,
e = limite de turbidité acceptable ; la turbidité de l’eau filtrée atteint cette valeur pour un temps t1 où le cycle doit être arrêté.
mesure et évolution de la perte de charge totale
On établit le graphique donnant l’évolution de la perte de charge P en fonction du temps (courbe a sur la figure 39). Par construction, il existe une perte de charge maximale que le filtre ne pourra dépasser : par exemple P2 = 200 hPa (2,00 m CE). Cette perte de charge est atteinte après un temps t2.

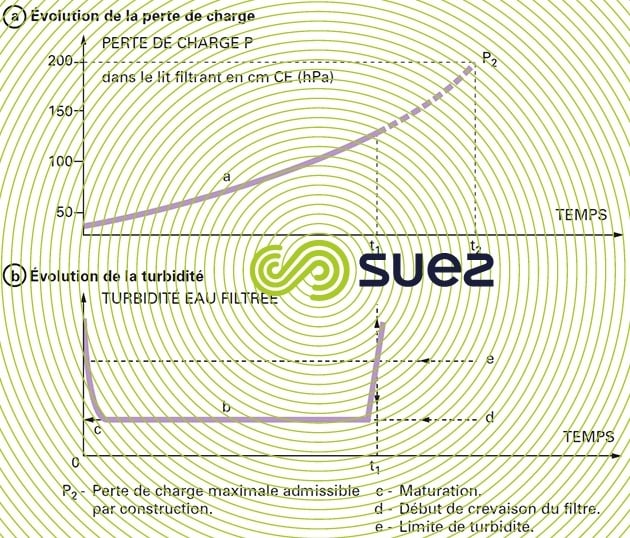

courbes de pression (diagramme triangulaire)
La partie a de la figure 40 représente un filtre ouvert à flux descendant, ayant une hauteur de sable égale à BD et une hauteur d’eau au-dessus du media de AB. Sur le graphique de droite sont portées en ordonnées les hauteurs des prises de pression A, B, C, D, au-dessus du plancher D du filtre, et en abscisses les pressions représentées en hauteur d’eau, avec la même échelle qu’en ordonnées. Ainsi au point B du filtre, situé au sommet du lit filtrant, la pression est toujours égale à la hauteur d’eau AB, reportée en B'b. Au point C du lit filtrant, quand le filtre est à l’arrêt, la pression a pour valeur AC, reportée en C'co ; de même, la pression statique au niveau du plancher est égale à AD reportée en D'do. Tous les points représentatifs de la pression statique aux différents niveaux du filtre sont sur la droite à 45° A'do. En tout point de la droite A'D', règne la pression atmosphérique.

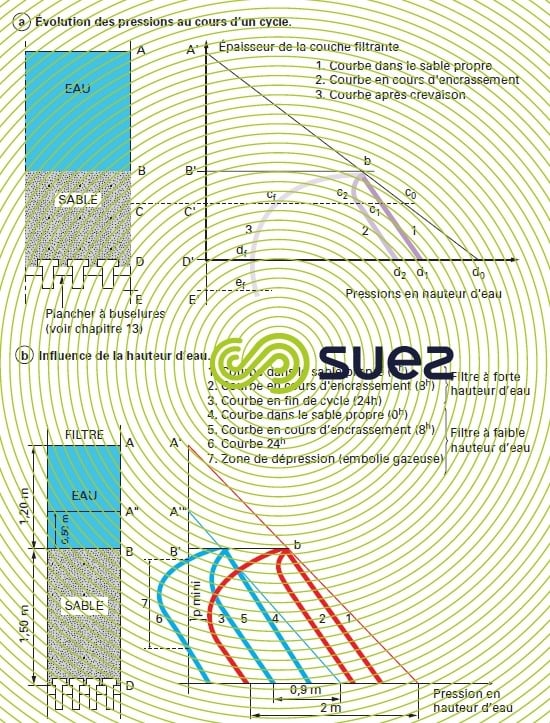

Une fois le filtre en service, et pour un sable homogène propre, la perte de charge est, d’après la loi de Darcy, proportionnelle à la hauteur de sable et au débit, admis constant pour cette analyse. La pression au point C du filtre devient égale à C'c1, la valeur cc1, représentant la perte de charge du sable entre les niveaux B et C ; de même, au niveau du plancher, la pression en D devient égale à D'd1, la perte de charge dans le sable propre étant dod1. La ligne bc1d1 est une droite puisque cc1 et dd1 sont proportionnels à la hauteur de sable (Darcy).
Quand le sable a achevé sa période de maturation, le report des pressions C'c2, D'd2 aux différents niveaux du sable donne la courbe bc2d2 représentative des pressions dans le filtre ; elle a une partie curviligne (bc2), correspondant à la couche encrassée, et une partie linéaire (c2d2), parallèle à la droite bd1 et représentative de la perte de charge dans la zone du filtre restée propre. Le point c2 figuratif du début de la perte de charge linéaire indique le niveau C atteint par les impuretés retenues dans le sable. Le point c2 caractérise donc la hauteur BC du « front de filtration » au temps considéré.
Le déplacement du point c2 au cours de l’encrassement représente l’avancement du front de filtration (courbe 3). Dans le cas de la figure 39a où le filtre ne donne plus d’eau claire quand la perte de charge maximale P2 est atteinte, la courbe représentative des pressions aux différents points du filtre est donnée par bcfdfef sur la figure 40a : elle atteint le plancher sans avoir de partie linéaire, c’est-à-dire que le front de filtration a dépassé le plancher et que le filtre est déjà crevé (t2 > t1).
Si on avait travaillé avec un filtre ayant une hauteur de sable plus importante, la courbe représentative de la pression aux différents points du filtre pour la perte de charge maximale disponible serait devenue linéaire au point ef : on en déduit la hauteur minimale DE de sable qu’il aurait fallu ajouter pour que t1 = t2 (figure 40a).
L’expérience montre que les valeurs de t1 correspondant à différentes hauteurs d’un sable défini sont sensiblement proportionnelles aux épaisseurs correspondantes.
colmatage de surface et colmatage en profondeur
Les figures 39 et 40a illustrent un cas avec colmatage en profondeur (un colmatage qui dans ce cas va même au-delà de la limite inférieure de la couche filtrante, traduisant un phénomène de crevaison).
La courbe 6 de la partie b de la figure 40 au contraire montre un cas avec colmatage de surface. Ce phénomène peut être provoqué par la filtration de floc très colmatant. Il peut aussi être lié à la nature du matériau, mal adapté (trop fin). La zone 7 est le siège d’une dépression pouvant entraîner un dégazage, d’où une réduction de la porosité ε (voir équations de base) et donc une perte de charge supplémentaire raccourcissant le cycle de filtration alors qu’une partie du lit filtrant n’est pas utilisée. La hauteur d’eau au-dessus du sable intervient également (voir filtration).
Le cas optimal consiste à tenter d’utiliser presque toute la couche filtrante, mais sans crevaison (courbe 3 de la partie b de la figure 40).
optimisation du fonctionnement
Pour une eau coagulée avec un sel métallique, t1 et t2 sont donnés par des formules empiriques, indiquant la variation de t1 et t2 en fonction des caractéristiques de construction et de fonctionnement :
- t1 = a · v–0,95 · K0,75 · D–0,45 · L0,95 · V–1,85 ;
- t2 = b · v–0,75 · K–0,7 · D1,5 · P0,9· V–0,65
avec :
D : taille effective du matériau,
L : hauteur de couche,
P : gain de perte de charge disponible (pour atteindre P2),
V : vitesse de filtration,
K : coefficient de cohésion du floc retenu (voir essais de traitabilité),
v : volume de matières en suspension floculées de l’eau à filtrer (après 24 h de sédimentation).
Les coefficients a et b sont expérimentaux. Ces formules permettent, à partir d’un seul essai de filtration, de prévoir les différents temps t1 et t2 correspondant à diverses conditions opératoires.
Pour maintenir une qualité d’eau filtrée correcte, il importe que le filtre atteigne sa perte de charge P2 correspondant au temps (t2) avant d’avoir crevé au temps (t1), c’est-à-dire que t1 > t2. Mais pour optimiser économiquement, il est souhaitable que l’écart entre t1 et t2 soit faible et donc que t1/t2 soit légèrement supérieur à 1 ; or la division de t1 par t2 donne :
On voit que pour une hauteur de lit donnée, la taille effective du matériau filtrant et la cohésion du floc retenu sont les paramètres essentiels de la variation de t1/t2, puisqu’ils sont affectés des exposants les plus élevés.
capacité maximale de rétention d’un filtre
Les matières en suspension se logent entre les grains du matériau filtrant. Étant donné qu’il faut toujours laisser un passage suffisant pour l’écoulement de l’eau, on ne peut guère espérer remplir plus que le quart du volume total des vides du matériau.
Dans un volume de 1 m3 de matériau ayant un bon coefficient d’uniformité (< 1,5), il y a environ 450 litres de vide quelle que soit la granulométrie ; le volume utilisable par les particules à retenir est alors de l’ordre de 100 litres, sous réserve que la taille effective du matériau filtrant et la perte de charge prévue par construction soient adaptées à la nature de ces particules.
Lorsque le filtre est à fonctionnement gravitaire (filtre ouvert) et que les matières en suspension à retenir sont à base de floc d’hydroxyde, la teneur en MS de ce floc (c’est-à-dire de la boue comprimée dans les interstices du matériau) n’excède pas 10 g · L–1 de sorte que la quantité éliminable par m3 de matériau filtrant est de l’ordre de 1 kg (100 L ×10 g · L–1 = 1 000 g).
Cette valeur augmente lorsque le floc est chargé de matières minérales denses (argiles, carbonate de calcium). Elle peut atteindre pour une boue à 60 g · L–1 de MS : 100 × 60 = 6 000 g.
Par exemple, un filtre de 1 m de hauteur de couche travaillant à la vitesse de 10 m · h–1, que l’on veut laver toutes les 8 heures (80 m3 d’eau par m3 de lit filtrant entre deux lavages), ne peut accepter plus de 1 000/80 = 12,5 mg · L–1 de MES floculées ou plus de 6 000/80 = 75 mg · L–1 de MES minérales denses.
Pour les matières en suspension des rivières, en filtration directe, la valeur est intermédiaire.
Dans le cas de filtration sous pression (par exemple filtration d’eau de mer ou de liquides industriels), la hauteur de couche peut atteindre 2 m et la perte de charge 0,5 bar, voire 2 bar. Sur des eaux chargées, on peut alors retenir dans le filtre des quantités de matières allant jusqu’à :
- CaCO3 : 4 à 15 kg par m2 de surface filtrante ;
- limon huileux : 10 à 25 kg ;
- battitures : 20 à 100 kg.
Ces ordres de grandeur permettent d’apprécier la teneur maximale en matières à retenir qu’il est raisonnable d’admettre dans l’eau brute alimentant un filtre, lorsqu’on a défini sa vitesse de filtration et la durée minimale du cycle entre deux lavages. Inversement, on peut en déduire la périodicité de lavage à prévoir pour une vitesse de filtration et une qualité d’eau à filtrer données.
choix d’un lit filtrant
Ce choix dépend de la nature de l’eau à filtrer (filtration directe d’eau brute, filtration d’eau décantée, filtration biologique d’eau résiduaire secondaire ou tertiaire) et de la qualité de l’eau que l’on désire obtenir. Il dépend également du type de filtre utilisé (filtre sous pression ou filtre ouvert) et de la perte de charge disponible. Le tableau 13 montre de façon sommaire l’influence la plus souvent observée de divers paramètres sur la qualité de l’eau et la durée des cycles.

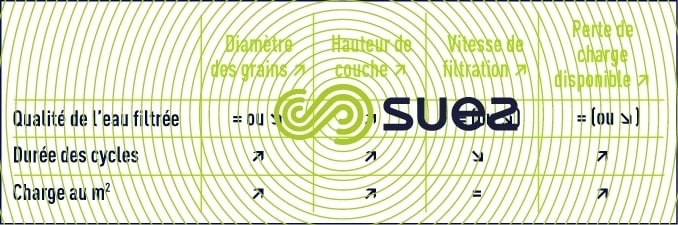

Dans le cas le plus général, le sens de filtration est descendant. Selon le type de lavage adopté (voir filtration) on distingue deux types de filtration qui correspondent à un choix de matériaux et/ou granulométries différents.
filtration sur couche de matériau homogène (sable en général)
Le lavage est effectué à l’air et à l’eau simultanément, sans expansion du lit. Il en résulte une homogénéité parfaite de la couche de filtration : la granulométrie du matériau filtrant reste la mêmeà la base et au sommet de la couche filtrante. Au cours du cycle, le front de filtration s’établit et progresse régulièrement, ce qui facilite la maîtrise du cycle de filtration. Dans la couche filtrante, l’évolution des courbes de pression est schématisée par les courbes 1, 2, 3 de la partie b de la figure 40 (colmatage en profondeur).
Cette figure illustre également l’influence de la hauteur d’eau au-dessus du média : un premier type de filtre (courbes 1-2-3) avec 1,2 m d’eau au-dessus du sable permet, pour y garder la pression positive minimale (voir p mini courbe 3), un encrassement de 2 m CE alors qu’un deuxième type (courbes 4-5-6) avec 0,5 m d’eau permet un encrassement de seulement 0,9 m CE (donc une durée de cycle beaucoup plus courte : de l’ordre de 8 h au lieu de 24 h dans le présent exemple). Si dans ce dernier cas, on essaie de pousser plus loin l’encrassement, la courbe représentative de la pression en profondeur passe partiellement de l’autre côté de l’axe représentatif de la pression atmosphérique (courbe 6), la partie correspondante du lit filtrant entre en dépression (voir zone 7) et une « embolie gazeuse » se développe alors au sein de ce lit.
Remarque : le lavage par eau seule avec fluidisation conduit à un classement du matériau (fines en partie supérieure) et donc à des cycles courts (colmatage de surface comme illustré par la courbe 6).
filtration sur plusieurs couches superposées (bicouche ou multicouche)
Pour favoriser la pénétration des impuretés dans toute la hauteur du filtre, on remplace une partie du sable par une couche de matériau plus léger (généralement l’anthracite) mais dont la taille effective est supérieure à celle du sable de la couche inférieure ; celle-ci sert alors de finition et de sécurité. Le choix de la granulométrie de chacune des deux couches doit être fait avec soin ; il faut en effet pouvoir les mettre en expansion de façon semblable avec le même débit d’eau de lavage, afin de pouvoir les reclasser à la fin de chaque lavage avant remise en filtration.
Cette disposition (dont la conception remonte au XIXe siècle) permet d’obtenir une meilleure répartition des MES : les plus grossières étant retenues dans la couche supérieure de grosse granulométrie, on peut ainsi augmenter la production d’eau filtrée par cycle, surtout dans les cas d’eaux contenant des MES très hétérogènes (cas typique des filtrations directes).
On peut également réaliser une filtration sur trois couches (ex. : anthracite ou pierre ponce, sable et grenat) ou davantage, ce qui permet d’augmenter la capacité de stockage des MES dans les couches supérieures et d’améliorer la qualité du filtrat, mais toujours au prix d’une grande rigueur dans les choix des matériaux et de la vitesse de lavage.
lavage du milieu filtrant
Le lavage est une opération très importante : lorsqu’il est insuffisant, il entraîne rapidement le colmatage permanent de certaines zones, ne laissant à l’eau qu’un passage réduit ; la perte de charge s’accroît alors plus vite, la filtration devient localement plus rapide et moins efficace (« renardage »).
Pour laver le matériau filtrant, on le soumet à un courant d’eau, circulant de bas en haut et réparti uniformément sur toute la surface du fond du filtre. Ce courant d’eau est destiné à détacher les impuretés (pour ce faire, le matériau doit recevoir une énergie suffisante) puis à les entraîner lavage par mise en expansion à l’eau seule (avec lavage de surface)
lavage par mise en expansion à l’eau seule (avec lavage de surface)
On choisit un débit d’eau suffisamment élevé pour mettre le matériau filtrant en fluidisation (fluidisation), ce qui suppose que son volume apparent augmente de 20 % au minimum.
Étant donné la variation de la viscosité de l’eau en fonction de la température, il est souhaitable dans certains cas de prévoir un système de mesure et d’ajustement du débit d’eau de lavage afin de maintenir en toute saison le taux d’expansion dans la plage désirée.
La couche en expansion est alors le siège de courants de convection, le matériau filtrant circulant vers le bas dans certaines zones et vers le haut dans les zones voisines ; cette circulation brasse le matériau et favorise le décollement des MES accumulées dans le filtre.
En revanche, il arrive que des morceaux de la couche compacte de boue (qui tend à former une croûte à la surface du matériau filtrant) soient entraînés en profondeur et, sous l’action des courants tourbillonnaires, forment des boules dures et volumineuses (mud-balls). On peut combattre cette tendance en brisant la croûte superficielle à l’aide de violents jets d’eau sous pression, distribués par des tuyères tournantes ou fixes (laveurs de surface).
Ce mode de lavage exige beaucoup de précautions et impose de mesurer la valeur de l’expansion du matériau filtrant. Son plus grave défaut est d’aboutir à un classement granulométrique du matériau, concentrant les fines en surface et donc défavorable (comme déjà vu, figure 40) à l’obtention de cycles longs ; en outre, la finition de l’eau est moins bonne, les grains les plus gros se retrouvant à la base du filtre.
lavage sans mise en expansion (par air et eau simultanés)
Une deuxième méthode, généralisée depuis les années 1950 chez SUEZ, consiste à utiliser un faible débit de retour d’eau, insuffisant pour provoquer l’expansion du sable, mais en l’agitant très énergiquement en même temps par une injection d’air surpressé. Le sable n’étant plus mis en expansion, il ne se classe pas et la croûte superficielle étant parfaitement détruite par l’air, les mud-balls ne peuvent pas se former ; de fait elles sont totalement inconnues avec ce mode de lavage.
- La période principale du lavage est la phase d’injection d’air et d’eau simultanément (phase dite de soufflage). C’est en effet pendant cette période que le matériau reçoit l’énergie la plus forte. La vitesse d’eau minimale à adopter pour un lavage efficace et la valeur maximale à ne pas dépasser pour éviter une perte de matériau filtrant dépendent à la fois de ce matériau et de la technologie du filtre. Cette vitesse est en général comprise entre 5 et 15 m · h–1. Quant à la vitesse d’air, qui détermine l’énergie de lavage, elle est le plus souvent comprise entre 40 et 60 m · h–1.
- Lorsque les impuretés ont été détachées du matériau filtrant et rassemblées dans la tranche d’eau qui sépare celui-ci de la goulotte d’évacuation, il faut « rincer », c’est-à-dire remplacer cette tranche d’eau boueuse par de l’eau claire. Cette phase est effectuée à l’eau seule à une vitesse de 15-20 m · h–1. Un balayage de la surface du filtre par un courant horizontal d’eau brute ou d’eau décantée conjugué au retour d’eau permet de réduire la consommation d’eau pendant cette phase (voir filtres à sable aquazur).
lavage à l’eau et à l’air, utilisés successivement
Ce lavage est utilisé lorsque la taille et/ou la densité du matériau filtrant ne permettent pas de mettre en œuvre, simultanément, l’air et l’eau de lavage sans risquer l’entraînement à l’égout par l’eau de lavage du matériau fin ou peu dense (Remarque : l’accrochage de bulles d’air sur les matériaux peut provoquer une véritable flottation des moins denses de ceux-ci) ; c’est le cas d’un lit filtrant constitué de sable fin (TE < 0,5 mm) ou de matériaux de faible densité (anthracite, pierre ponce, charbon actif, biolite), a fortiori une combinaison de ces matériaux (filtres multicouches). Dans la première phase de lavage, l’air est utilisé seul pour détacher du matériau filtrant les impuretés retenues.
Dans la deuxième phase, un retour d’eau à fort débit, assurant une mise en expansion du ou des matériaux filtrants, permet d’extraire du lit et d’évacuer les impuretés détachées lors de la première phase. C’est également cette mise en expansion qui, quand elle est suffisante (> 20 %), permet le reclassement des matériaux des filtres multicouches qui ont été mélangés pendant le soufflage. Dans le cas d’impuretés lourdes ou particulièrement difficiles à éliminer (eaux résiduaires, par exemple), on a avantage à répéter plusieurs fois ces séquences.
lavages particuliers
Les procédés de lavage décrits dans ce paragraphe ont l’avantage d’éviter la bâche de stockage d’eau filtrée, voire d’éviter également le stockage d’eau sale en produisant des eaux de lavage en continu.
lavage mutuel
Le lavage mutuel consiste à utiliser tout ou partie de l’eau des filtres restés en production pour laver le filtre colmaté. Il permet d’éviter la bâche de stockage d’eau filtrée et de simplifier considérablement la technologie de lavage (voir les filtres). Ce principe peut être appliqué avec ou sans soufflage à l’air.
lavage par compartiments
Dans le filtre, des parois fixes délimitent un grand nombre de compartiments unitaires de lavage. Contrairement aux lavages normaux qui concernent toute la surface d’une unité filtrante, ces compartiments sont lavés un par un successivement (ex. : filtres ABW).
Le lavage est réalisé à l’eau seule et sans air (l’eau de lavage étant fournie par les cellules adjacentes, c’est donc aussi un lavage mutuel). Ces filtres sont généralement employés avec des matériaux fins et une faible hauteur de couche.
filtration et lavage en continu (figure 41)

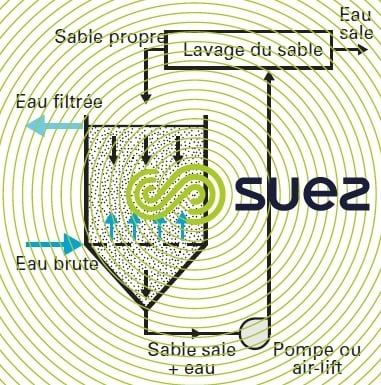

Le lit de sable est stocké dans un appareil formant trémie. Pendant la filtration, le sens de circulation de l’eau dans le lit de sable est ascendant.
Le sable sale est extrait à la base de la trémie et lavé dans un dispositif spécifique situé au centre de l’appareil ou à l’extérieur. La séparation « eau boueuse – sable » située à la partie supérieure du lit permet de redistribuer le sable propre en surface. Le lit descend de (par exemple) 10 à 20 cm · h–1, donc tout le sable est nettoyé en environ 6 à 15 h.
À cause de la pente de sa trémie, ce type d’appareil est limité en surface et se trouve donc dédié à des petits débits : petites stations en EP ou eau de procédé, ou en réutilisation des ERI ou ERU.
fréquence de lavage et consommation d’eau de lavage
La fréquence des lavages dépend des divers paramètres jouant sur t1 et t2.
La consommation d’eau par lavage (4 à 10 m3 par m2 de surface filtrante) est essentiellement fonction de la nature et du poids des particules retenues par m3 de matériau filtrant ainsi que de la méthode de lavage. En particulier, l’utilisation conjointe d’air de lavage et d’eau de balayage non filtrée permet de réduire d’environ 20 à 40 % la consommation d’eau par rapport au lavage à l’eau seule.
La consommation d’eau de lavage est d’autant plus forte que :
- la hauteur d’eau au-dessus du matériau filtrant est plus grande ;
- les goulottes d’évacuation des boues sont plus écartées les unes des autres ;
- la quantité de boues à évacuer est plus grande ;
- la cohésion et la densité des boues sont plus fortes.
Cette consommation est également accrue lorsqu’on utilise des laveurs de surface.
applications
filtration rapide à flux descendant
Selon le cas elle se met en œuvre dans des appareils ouverts (à écoulement gravitaire) ou fermés sous pression (voir les filtres) à des vitesses allant de 4 à 50 m3 · h–1 · m–2. Dans les filières de traitement physico-chimique, c’est le type de filtration le plus courant. On l’appelle rapide par contraste avec les anciennes installations de filtration lente (de l’ordre de 5 m · j–1).
En traitement d’eau potableou de procédés on distingue habituellement :
- la filtration directe sans coagulant ;
- la filtration avec « coagulation sur filtre » (CsF) d’une eau non décantée au préalable ; les réactifs utilisés peuvent être un coagulant, un adjuvant de floculation et un réactif d’oxydation ;
- la filtration d’une eau coagulée et décantée ou flottée ; dans ce dernier cas, les filtres se trouvent alors dans la situation idéale consistant à recevoir une eau de qualité pratiquement constante et faiblement chargée. Les vitesses de filtration peuvent s’échelonner entre 7 et 20 m3·h–1·m–2 suivant la qualité de l’eau décantée et la nature des filtres utilisés. On peut alors couramment obtenir à 15-20 °C une production d’au moins 250 m3 par m2 et par cycle ; avec une consommation d’eau de lavage typique de 5 m3·m–2, la perte en eau est limitée à moins de 2 %.
On peut également utiliser deux filtrations en série, chaque étage de filtration pouvant être précédé d’une coagulation, avec addition d’adjuvant et d’oxydant.
Dans certaines réalisations récentes, le traitement se fait dans des conditions qui vont aux limites des possibilités de ce type de filtration, comme c’est le cas de la CsF de Sydney en Australie (voir filtres à sable aquazur et la clarification) dont les paramètres de base sont les suivants :
- la vitesse maximale de filtration est élevée (24 m · h–1) sans nuire à la qualité d’eau filtrée qui est toujours excellente (< 0,1 NTU) ;
- le matériau est du sable homogène de grosse granulométrie (TE = 1,8 mm) avec une forte hauteur de couche (2,1 m). Le filtre à sable homogène a été choisi de préférence à un filtre bicouche pour des raisons de coût de réalisation mais aussi d’économie sur les volumes d’eau de lavage ;
- les réactifs injectés sont du chlorure ferrique et deux polymères (l’un cationique et l’autre anionique) qui conduisent à un floc très résistant et colmatant ;
- un lavage « haute énergie » avec air et eau simultanés est mis en œuvre.
La filtration tertiaire des eaux résiduaires peut se réaliser dans des conditions analogues à celles décrites ci-dessus pour les traitements d’EP
autres types de filtration
Bien que le courant descendant représente la solution technique la plus logique pour les lits filtrants à matériau plus lourd que l’eau, il existe aussi des appareils où le sens de filtration est différent :
filtres à flux ascendant
L’eau percole dans le milieu filtrant de bas en haut. Le classement granulométrique après expansion (lavage) est plus favorable au passage de l’eau et la perte de charge est diminuée. Par contre le risque de crevaison est important et ne permet pas d’avoir ce type de filtre en dernière étape de la filière. ; au-delà de cette limite, le matériau s’expanse et le filtre crève. Afin d’éviter cet inconvénient, il est nécessaire de prévoir la mise en place d’un système de blocage du matériau filtrant (par exemple une grille…) ou de choisir un filtre à sable homogène et lavage continu.
filtres à lit flottant (figure 42)
Pour conserver l’avantage du courant ascendant, tout en évitant les inconvénients des filtres à sable basés sur ce principe, on peut adopter un milieu filtrant constitué d’un matériau flottant (plus léger que l’eau), par exemple du polystyrène expansé (Médiaflo). Un tel filtre est lavé sans utilisation de réserve d’eau de lavage, par simple chasse de la tranche d’eau présente au-dessus du lit filtrant (les pertes d’eau traitée pour le lavage sont limitées à 0,8 m3 · m–2).
Toutes choses égales par ailleurs, le filtre à lit flottant donne les mêmes résultats qu’un filtre à sable (voir aussi filtres filtrazur).
Il peut être appliqué en traitement d’eau potable ou en traitement tertiaire d’ERU.

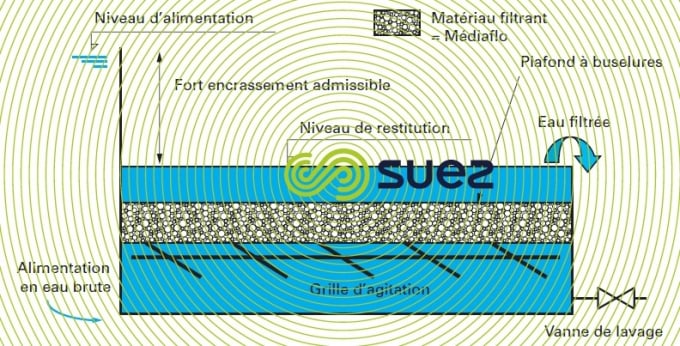

filtres à double sens de filtration
L’eau à filtrer pénètre dans le matériau filtrant à la fois par la partie supérieure et la partie inférieure de ce matériau ; la reprise d’eau est effectuée au sein de la masse filtrante. Cette solution, très compacte, a connu dans le passé quelques applications.
filtres à flux horizontal
Cette technique est parfois mise en œuvre dans de petites stations très rustiques (ex. : filtres dégrossisseurs à gravier).
filtres biologiques
En eau potable, il existe de nombreuses applications où l’effet recherché est basé principalement sur des phénomènes biologiques :
- filtration lente des eaux naturelles de surface ;
- déferrisation-démanganisation biologique des eaux souterraines ;
- transformations de l’azote (nitrification ou dénitrication) dans les eaux naturelles ;
- minéralisation du carbone biodégradable sur des filtres à charbon actif.
Les éléments spécifiques à ces différents types de filtration seront passés en revue dans les applications du génie biologique en traitement des eaux potables.
En eau résiduaire, une simple filtration tertiaire bénéficie déjà de l’activité biologique des MES retenues, mais c’est dans le domaine des Biofiltres traitant les pollutions carbonées et/ou azotées que ces dernières décennies ont vu les développements les plus spectaculaires. Ces biofiltres, aérés ou non, où les phénomènes biologiques sont prépondérants par rapport à l’effet de filtration, seront décrits pour leurs principes au niveau des cultures fixées et pour leur technologie aux filtres biologiques.
Outil Marque-page
Cliquez sur l'outil marque-page, puis surlignez le dernier paragraphe lu pour pouvoir poursuivre ultérieurement votre lecture.
